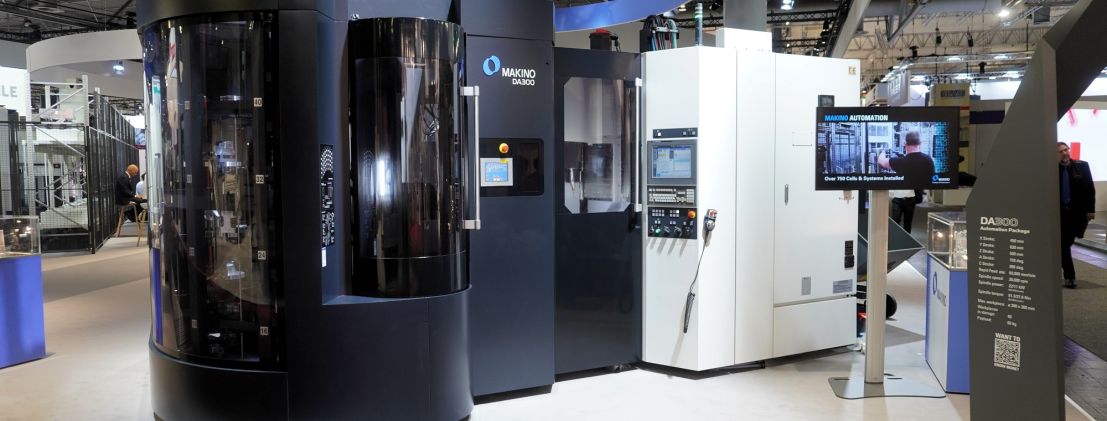
Makino Develops DA300 Automation Package for Smaller Job Shops
In smaller job shops where each job is different, automation solutions require a higher degree of flexibility. And as space is often limited, any automation solution needs a compact footprint. Makino has specifically developed the DA300 automation package for smaller job shops. Despite its compact dimensions, the DA300 automation package displays a high degree of autonomy and performance.
The DA300 has established a strong position in the 5-axis vertical machining market. Its dynamics have boosted its users’ production performance in markets ranging from aerospace to semiconductor components. Now, Makino has packed all its expertise and the experience gained from seeing the DA300 in action to custom-design a version for this automation package.
Polygonal taper interface
A distinct polygonal taper interface ensures maximum rigidity and minimum hassle in automated production. This industry-first type of work-holding pallet maximise space utilisation and can hold parts as big as 300 mm in height and 360 mm in diameter with a maximum payload of 60 kg. The unique design enables parts to be automatically positioned in the working area with a repeatability of under 2 micron.
Big tool magazine
As one of the target markets is medium-mix production environments, the automation package comes with a double-ring magazine that minimises tool preparation time and can hold up to 118 tools. For high-mix production scenarios an optional external magazine with up to 254 tools maximises the number of tool types available. Despite a footprint of just 6 x 3.75 metres this automation package can accommodate up to 40 work-holding pallets. And when loading pallets into the machine, two waiting stations help minimise pallet changing times and cleaning times while waiting.
Simple but powerful software
As no automation package is any good without good software, Makino has simplified the user interface (UI) and maximised the system’s functionality by placing the automation interface inside the familiar Professional 6 controller. Pallet management has never been easier. Thanks to the simple but powerful UI, operators can access all the machine features from the same screen, e.g. set up materials, put different jobs on each pallet, set priorities, place urgent requests, and monitor and manage production status.
GI breaker
With the launch of this automation package comes a new feature on the DA300, a GI breaker. One of the worst problems a machinist faces is handling the big, long chips from complicated drilling operations. The existing cycles to avoid these chips greatly increase cycle times and tool wear. This breakthrough technology has introduced micromovements into the drilling operation to break the chips into small pieces – and do that with without impacting the cycle time or tool life. The GI breaker will improve process reliability and help manufacturers sleep more easily when a DA300 is left working overnight or at weekends.
Enhance reliability
The new eStabilizer technology has been introduced to further enhance the machine’s reliability. Though a set of sensors strategically positioned around the machine it measures the shop floor temperature and compensates for any tiny changes, thus ensuring the machine’s accuracy is unaffected. This enhancement of the DA300’s already outstanding thermal stability makes the machine even more reliable in harsh ambient conditions.
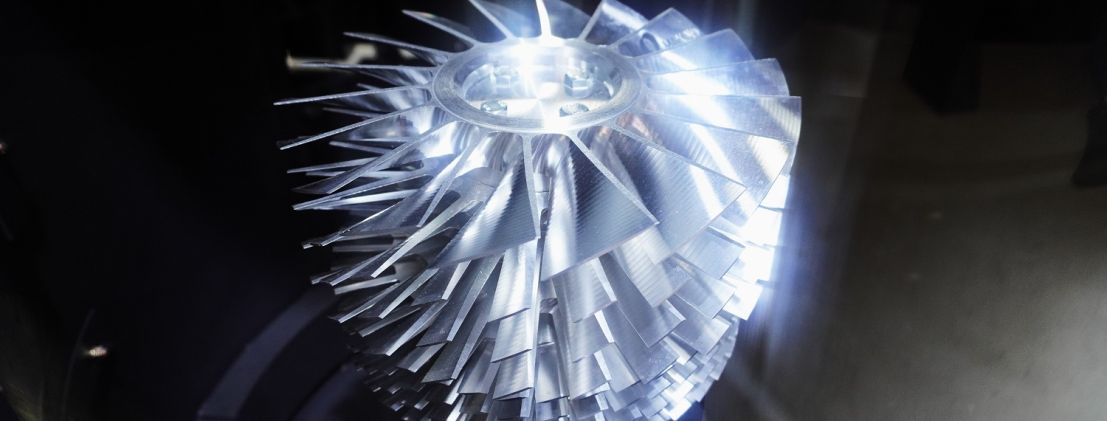