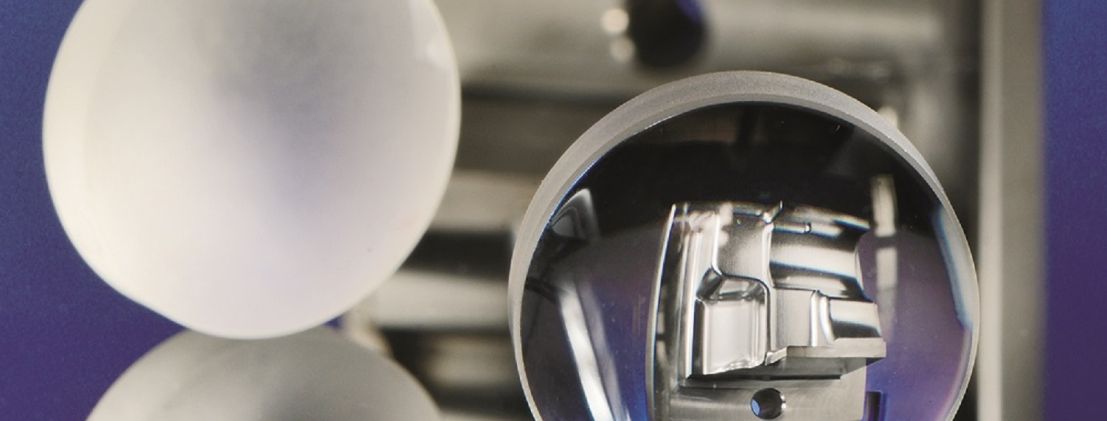
Laser proves convenient alternative to mechanical polishing and deburring
The 5th Conference on Laser Polishing LaP has delivered impressive results regarding laser-based alternatives for polishing components made of glass, metal and plastic. More than 70 experts from all over the world met in October 2022 to discuss the state of the art laser deburring and laser polishing technologies as well as on related topics such as metrology and process control.
It's all in the mix: On the first day, LaP number 5 was aimed primarily at companies that manufacture optical surfaces and polish glass as well as plastics. The event kicked off with a presentation from Jena, one of the international centers for glass and optics manufacturing: Anett Jahn, managing director of the company ShapeFab, and Thomas Schmidt, laboratory engineer at the Günter Köhler Institute for Joining Technology and Materials Testing (ifw), encouraged LaP participants to begin using laser polishing. ShapeFab and ifw combine CNC milling and laser-based processes to polish optical surfaces up to 250 mm x 400 mm in size. This hybrid method should soon be able to process any contour and even complex free-form surfaces reliably, quickly and cost-effectively. The company and institute presented a large complex demonstrator component, which was produced in a total of around seven hours, of which about only 10 minutes were spent on laser polishing; the conventional mechanical polishing process would have taken up to ten hours. In the next step, the group now wants to further reduce the CNC machining time.
In Jena, process monitoring of the laser with a pyrometer plays an important role. Digital monitoring with this measuring instrument is also used by Manuel Jung from Fraunhofer ILT, who presented the setup of a low-noise closed-loop control for laser polishing of optics at LaP. The scientific member of Willenborg’s team recommended the use of software that allows laser polishing to be carried out reliably with a maximum temperature deviation of less than 0.5 percent. In this way, the Aachen team was able to reduce waviness (MSFE) by as much as a factor of 10. The scientist hopes for further improvements as the institute is developing a thermally even more stable and low-noise control process that no longer uses a pyrometer, but rather a thermocamera and sophisticated statistical methods.
Producing free-form surfaces with the ultrashort pulse laser
How femtosecond lasers can be used to correct the shape of glass components with nm height resolution was reported by Dr. Jie Qiao, Associate Professor from Rochester Institute of Technology, USA. The secret to success lies in a dynamic mathematical model that can predict ablation and temperature evolution. Energy density serves as a measure to scale the process further. Demonstrated on flat samples, the process is now paving the way for the high-precision production of even more complex surfaces.
The subnano range was also the focus of Emrah Uluz, a research associate from Fraunhofer ILT who works on laser beam figuring LBF. His presentation focused on using nanometer-precise ablation to reduce the waviness of polished fused silica surfaces. A key factor here is a highly stable laser operating at constant laser power (standard deviation: ≈ 0.1 percent).
Classic mechanical polishing of glass repeatedly results in smaller and larger scratches that impair its surface quality. According to Dr.-Ing. Kerstin Götze, group leader of laser polishing at Ernst Abbe University in Jena, 99.9 percent of these scratches can be reliably removed with the CO2 laser – especially when it operates at a low feed rate. The process has proven particularly effective in improving the quality of curved and structured surfaces.
Green laser removes “subsurface damage”
Professor Jiwang Yan from Keio University in Yokohama, Japan observed that thermal effects during classical mechanical polishing of single-crystalline silicon wafers cause damage just below the surface. The Japanese experts succeeded in repairing this “subsurface damage” without material ablation and environmental pollution by remelting with green laser light: The remelted layer grew single-crystalline onto the underlying material. However, this was only successful after prior simulation of the molecular structure. After the successful experiments, various laser systems were developed in Yokohama that are suitable not only for repairing surfaces but also for creating functional surfaces.
An interesting phenomenon inspired scientist Dr. Bowei Luo from the Shenzhen Institute of Information Technology in China to combine cold and hot laser polishing of silicon carbide. Polishing this ceramic material with a UV laser lowers the surface roughness to 1.4 µm at a laser power of 15 watts. However, the surface roughness can be further reduced to 1.082 µm by preheating the ceramic to 1400 °C with an IR laser. Yet this also requires adapting and optimizing the “cold” UV laser process to the “hot” IR process. According to Dr. Luo, the shape of the laser beam plays a key role: For example, a uniform top-hat laser beam with a diameter of 0.32 to 0.54 mm could effectively reduce thermal shock, especially at the edge polishing areas.
The shape of the laser beam also concerns scientist Karsten Braun of Fraunhofer ILT. He developed process strategies for 3D-printed plastic parts whose roughness Sa varies from 14 µm (PA12) to 42 µm (PEEK) depending on the material. When polishing with a 120 W CO2 laser in the mid-IR range (wavelength: 10,600 nm), Braun relies on fast quasi-top-hat scanning (5 to 10 m/s) from a large distance (100 to 1000 mm). The scanning process runs up to 20 times and is temperature-controlled. Depending on the material, the roughness Sa after laser polishing is 0.8 to 0.25 µm.
The second day of the conference was directed primarily at companies that process conventionally manufactured or 3D-printed components made of metal. A very challenging task was presented by Dr. Safak Nelsi, an assistant professor from the OSTİM Teknik Üniversitesi in Ankara, Turkey. He reported on the laser polishing of an aerospace component (Ti48AL2Cr2Nb) produced using the electron beam melting process (Arcam A2X EBM). In a joint project with an industrial partner, he succeeded in reducing the often very rough surfaces of an additive-manufactured component by around 95 percent to as little as 1.6 µm. A 600 W IPG fiber laser (wavelength: 1070 nm) was used; it polished the surface at a scanning speed of 220 mm/s. Challenges during the tests were surface cracks, waviness and oxidation.
Laser polishing in keyhole and conduction mode
Prof. Dr. Frank E. Pfefferkorn from the University of Wisconsin-Madison together with the Bremen Institute for Applied Beam Technology BIAS dealt with the typical problems of components produced additively in a powder bed using the laser powder bed fusion (LPBF) process: Components made with LPBF often have a poor surface quality due to partially adhering particles, layer effects and balling. In experiments with a component made of cobalt chrome (Stellite 21), the German-American team found that laser polishing in conduction mode (CM), which is commonly used, has limitations. In contrast, laser polishing in keyhole mode (KM) produced the best results – reduced roughness and waviness – with the final polishing step being performed by a CM process.
The surface roughness of metal components produced with laser-based 3D printing processes, i.e. LPBF, can be reduced by laser polishing. Waviness is still an issue, however, as Laura Kreinest, a Fraunhofer ILT employee, discovered during laser polishing of an LPBF component made of 1.2343 tool steel. Even after 16-fold laser polishing, the waviness Wa was still around 1 µm. The scientist solved the issue using the “WaveShape” process developed at the institute, which creates the inverse structure of the undesired waviness on the metal surface by laser remelting, thus reducing the waviness.
Laser increases fatigue life
How laser polishing influences the fatigue behavior of LPBF components made of Inconel 718, a well-known aerospace material, was investigated by Professor Yingchun Guan from Beihang University in Beijing. She pointed to an older study presented at LaP 2020 using turbine components in which laser polishing reduced Ra roughness from more than 10 to less than 0.1 µm. New analyses have now shown that the mechanical properties have also improved: Laser polishing increases the fatigue life at a mechanical stress of 840 MPa by 15 to 20 percent compared with the values for milled surfaces; at 500 to 600 MPa, it is just as high.
Special materials such as advanced high-strength steels are interesting for lightweight construction in the automotive sector since they have high strength (>1000 MPa). However, microdefects often occur at the edge during shear cutting or laser cutting, making the components susceptible to edge cracking. Scientist Dongsong Li from the Institute of Ferrous Metallurgy (RWTH Aachen University) presented a process for deburring and edge rounding using laser radiation, which was developed in collaboration with Fraunhofer ILT. The laser melts the edge, removes the micro-defects and smooths it. In the experiment, a 4 kW CW diode laser successfully processed a 1.5 mm thick sheet of high-strength dual-phase steel (strength: 1000 MPa) at 3.6 m/min. Hole expansion tests and diabolo tests show significantly improved performance after laser treatment. This process makes it possible to improve forming capacity by more than 200% before the first edge cracks appear.
Process monitoring is playing an increasingly important role in laser polishing: Dr. Evgueni V. Bordatchev, team leader at the National Research Council of Canada in London (Ontario), and Sven Linden from Fraunhofer ILT reported on German-Canadian cooperation in this field. In order to automate the setup of a polishing process, they integrated a white light interferometer (WLI), which detects surface structures with high precision, into a laser polishing machine. Also as part of the collaboration, a high-speed thermographic camera was integrated into another machine. The real-time data from the camera is used to close the control loop and adjust the parameters. Visibly fascinated, the LaP guests watched the video of a high-speed camera which, at 42,000 frames per second, visualized the solidification of liquid hot-work tool steel (1.2343) in the melt pool.
The thermal camera was used by Daniel Beyfuss, a scientist at the University of Western Ontario in London, Canada, to monitor laser remelting (LRM) processes. The Canadian used coaxial optical measurement to analyze the effects of thermodynamic instabilities on the LRM process. An important result is the fundamental role of the thermodynamic equilibrium between applied laser power and its conversion into remelting processes because it significantly influences the process stability.
Melt-pool analysis in the synchrotron
US scientist Patrick J. Faue from the University of Wisconsin-Madison reported on a research project with the Bremen Institute for Applied Beam Technology BIAS. They are focusing mainly on high-speed X-ray imaging in the synchrotron at the renowned Argonne National Laboratory (ANL), an approach that offered interesting insights into melt-pool dynamics during laser polishing. For example, the research team observed how melt-pool oscillations form and, thus, affect the keyhole.
Satisfied LaP initiator and moderator Dr. Willenborg from Fraunhofer ILT stated after the virtual LaP: “Sixteen presentations covered various aspects from classical glass polishing to melt-pool analysis in a synchrotron over two days. The mixture really makes the difference: This is probably why almost all 70 participants were present online throughout the entire conference. Despite the virtual success, however, I look forward to seeing the international laser polishing community again at the sixth LaP, which will then hopefully take place live in Aachen again in 2024!”