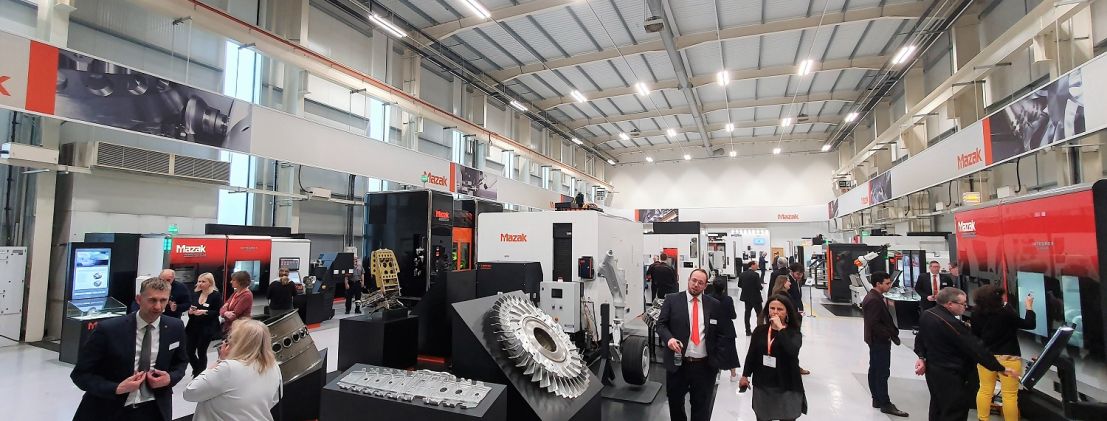
Large-scale investment leads to efficiency, productivity and sustainability at Mazak
14 million euros have been invested in Mazak's European factory in Worcester, UK, over the past five years, and a further 5 million euros worth of new production machinery is also on the agenda this year. The reason for the investments has everything to do with the commitment to an efficient, sustainable and productive factory.
Mazak organised an event for the international trade press in mid-April to present the latest news and the revamped production plant. The Mazak factory in Worcester is one of 10 manufacturing sites in the world and has been producing different types of machine tools, including CNC lathes, vertical machining centres and five-axis machines, since 1987. In total, more than 30,000 machines have already left the plant. Currently, the plant has a capacity of 100 machines per month. This is enough to fill about 50% of Europe's machine needs. The Worcester plant now produces 300 different machine versions, including the Quick Turn VCE, VCN, VTC and CV5-500 series.
Innovation in machining
A key part of the plant is the machining department. Here, five horizontal machining centres process castings 24/7, which are supplied and removed via a 100-meter-long FMS system with space for 650 pallet positions. Over the next three years, these machines, now 15 years old, will be replaced. "Our customers place the highest demands on our solutions, especially when it comes to quality, reliability and accuracy. We can only meet these requirements if our own machine park with so-called 'mother machines' is up to scratch. That is why we continuously invest in our own production," says Richard Smith, European Group Managing Director at Mazak.
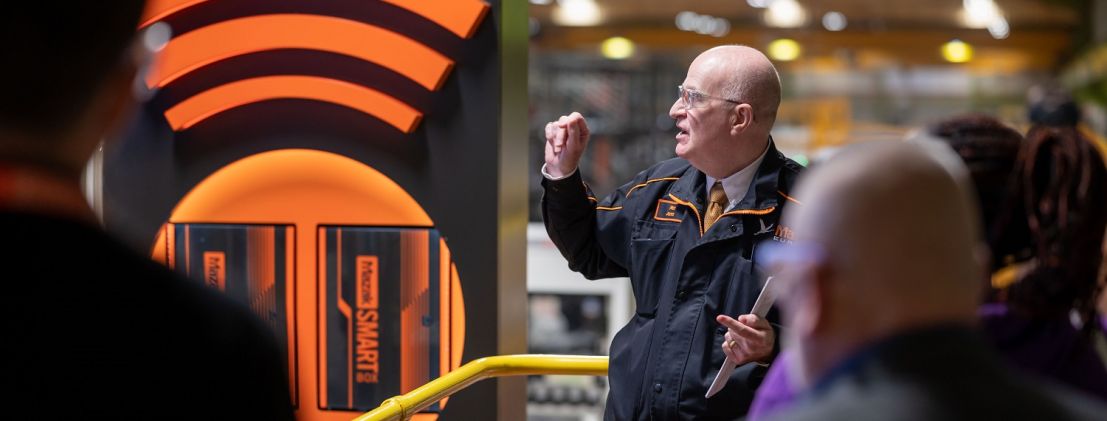
Increasing production efficiency
At Mazak, process optimisation is high on the agenda. Therefore, the machine builder has extensively automated and digitised its Worcester plant to maximise production efficiency. For this reason, the machining department was recently expanded with two new machining centres, an Integrex i-400S and an Integrex i-300S. Both multitasking machines are connected to a RoboJob Tower. The complete cell enables unmanned production on a relatively small floor space.
In addition, Mazak uses various Industry 4.0 solutions to gain more insight into the production process. Interestingly, these solutions are also simply available to customers to make their production smarter. Mazak uses the SmartBox, which is connected to all machines and production equipment in the factory via MTConnect, as the basis for this. SmartBox allows advanced cybersecurity to collect data from the production process. After analysis, this data can be used to improve productivity and quality.
For monitoring and analysis, Mazak uses Smooth Monitor AX. This solution monitors and analyses the operational status of all machines and tools in the factory. The results of each machine are visualised graphically. This information is used to adjust the process or design it more efficiently. Besides the status of machines, Smooth MONITOR AX also provides insight into tool life, maintenance status and energy consumption. Furthermore, Mazak uses Smooth Scheduler. This system helps to gain insight into production planning and make better use of machine capacity. Thanks to this solution, it is possible to look months into the future, making it even easier to predict available machine capacity and expected delivery times. All solutions together ensure faster lead times, better use of resources, less downtime and higher quality.
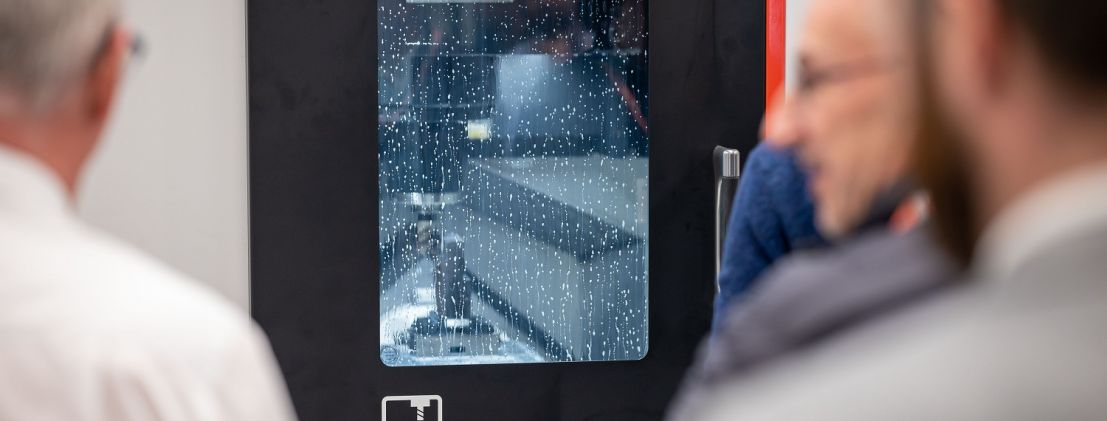
Spindles made in-house
In addition to parts production with the FMS line, all spindles are also produced in Worcester. This takes place in a conditioned room where the spindles are ground with Studer grinding machines. The essential parts of the spindle achieve an accuracy within 3 micrometers. Mazak recently commissioned three new grinding machines to modernize the grinding department, including an S41 and S151 from Studer. The advantage of these machines is that they offer more machining possibilities. For instance, they can also grind threads and conical surfaces. "This kind of machining used to be outsourced. The disadvantage was the long and varying delivery time. With the new grinding machines, we can now machine the threads and tapered surfaces in half an hour, while keeping the work in-house and therefore monitoring quality better," Smith says.
Furthermore, the spindle department repairs 100 spindles every month, spindles from new to old machines and spindles from simple turning centres to the more complex five-axis and Integrex multitasking machines. The spindles are extensively tested and checked for temperature and vibration during and after repair and then delivered back with the same warranty as a new spindle. They also investigate the cause of a broken spindle so that they can improve it again in the future. There are now as many as 50 technicians working in the spindle department. This number has grown since Smooth spindles were introduced and the demand for fast multitasking machines increased. "In recent years, machines have become much faster and are operational for many more hours in a day due to automation. This has the benefit of significantly increasing productivity at our customers. However, the consequence is that machine components such as spindles require earlier maintenance. Moreover, modern multitasking machines are equipped with multiple spindles and, in addition, we see that the number of collisions is increasing due to the shortage of quality craftsmen. All in all, this is causing a sharp increase in service needs."
Looking at European market
In addition to the factory, Worcester is also home to a design and engineering team, who specifically research the needs of the European market and develop new solutions and machine tools for it. The compact, five-axis CV5-500 is a great example of a machine tool developed specifically for the European market and manufactured in the UK. Lawrence McCann, Engineering Director European Group, says: The design and engineering team gets input from our service and salespeople. They are close to the market and see what customers need. Based on those insights, many great ideas have already come to fruition."
Sustainability is hot topic
In addition to making the necessary investments in modernising the machinery at the Worcester plant, Mazak has also made a big deal with sustainability in mind. That all started in 2019, when the machine builder presented some lofty sustainability goals at the EMO in Milan to anticipate the ambitions of the Paris climate agreement. "At the moment, the climate agreement does not provide exact guidelines specifically for the machine tool industry. Therefore, we have drawn up our own plan of action that closely follows the ambitions of the climate agreement. As a family business with a view to the future, we see preventing climate change as a moral obligation. Moreover, being frugal with energy is ingrained in Japanese culture, as they have few energy resources of their own in Japan. Mazak has put its sustainability goals and solutions under the 'Go Green' initiative," says Smith.
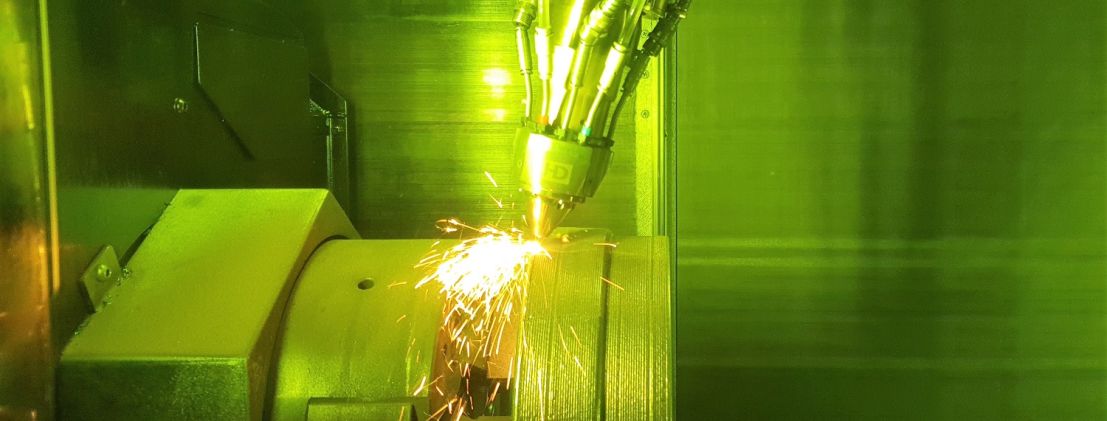
Small adjustments, big savings
Mazak aims to drastically reduce its carbon footprint over the next seven years. To reduce CO2 emissions in its own operations, Mazak has made many strides globally. For instance, offices and production sites have been fitted with solar panels for power generation and production processes have been modified to be more energy efficient. At the Worcester plant alone, energy consumption has been reduced by 43%. "It's very small adjustments that you didn't think about before," says a production manager during a tour of the Worcester plant. "New machines are first tested for 24 hours before they go on transport to check that the assembly was completely flawless. Such a machine used to remain on standby at weekends after a test-run. Nowadays, a timer ensures that the machine is switched off after 24 hours. Thanks to small adjustments, such as turning off the compressor when not in use, big savings are possible across the board."
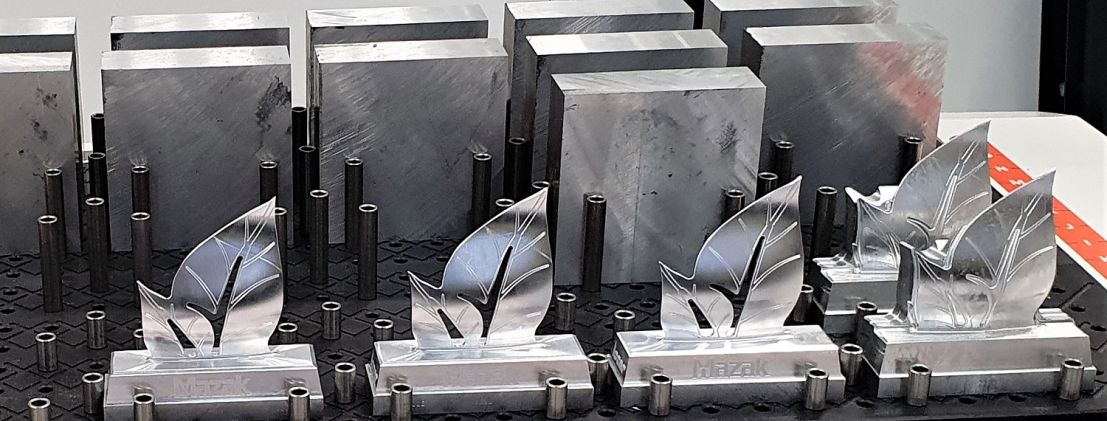
Economical and efficient machine tools
Smith: "The European manufacturing industry consumes some 1524 TWh of energy annually. To offset the associated CO2 emissions, as many as 15.7 million trees are needed. So we can make a big difference as an industry if we can reduce energy consumption. In this, machine builders have an important role to play. After all, we can make our own factories more sustainable, but the biggest impact we can realise if, through economical and efficient machine tools, we bring down energy consumption at all our customers." Meanwhile, Mazak has made several developments to make machine tools more energy efficient. For example, energy-hungry components such as transformers, cooling units, high-pressure pumps and hydraulic and pneumatic systems have been replaced or modified for more economical solutions. For example, the new generation of the five-axis Variaxis i-800 NEO machining centre has already been designed according to the Go Green vision. Thanks to energy-saving technologies, the machining centre emits 22% less CO2 than the previous model. The QTE-300SG turning centre also features energy-saving components. As a result, this machine emits 7.7% less CO2. The ultimate goal is for Mazak's machines to have four times greater environmental efficiency than the 2010 benchmark by 2030.
Transition to green manufacturing
"For a long time, energy consumption was not really a topic in the manufacturing industry, but that has changed nowadays. The price of energy has increased enormously and, in addition, manufacturing companies will soon have to record how much energy was consumed when processing a workpiece. With Go Green, Mazak already has a solution to not only directly reduce energy consumption and CO2 emissions, but also to help customers record, analyse and optimise their energy consumption," says Van Berkel.
During EMO Hannover 2023, Mazak will put the Go Green initiative even more in the spotlight. Several new solutions will be on show then, including new features in the Smooth control that can help users transition to green manufacturing. In addition, the machine builder will give an insight into Mazak iConnect. In addition to machine-specific information such as manuals, maintenance videos, parts order history, and professional training packages, this web portal also provides the ability to connect machine tools to Mazak's secure cloud service. This new Machine to Mazak (M2M) solution allows users to monitor the operation of their machines online. In addition, it is possible to receive remote support from application and service engineers and iConnect can also be used for predictive maintenance purposes. "M2M is also a great way to increase sustainability. Because our application and service technicians can watch the customer remotely, far fewer transport movements are needed. It is also possible to schedule maintenance precisely, so that the machine always remains in optimal operation. All in all, we are on the right track to create a sustainable manufacturing industry," Smith says.
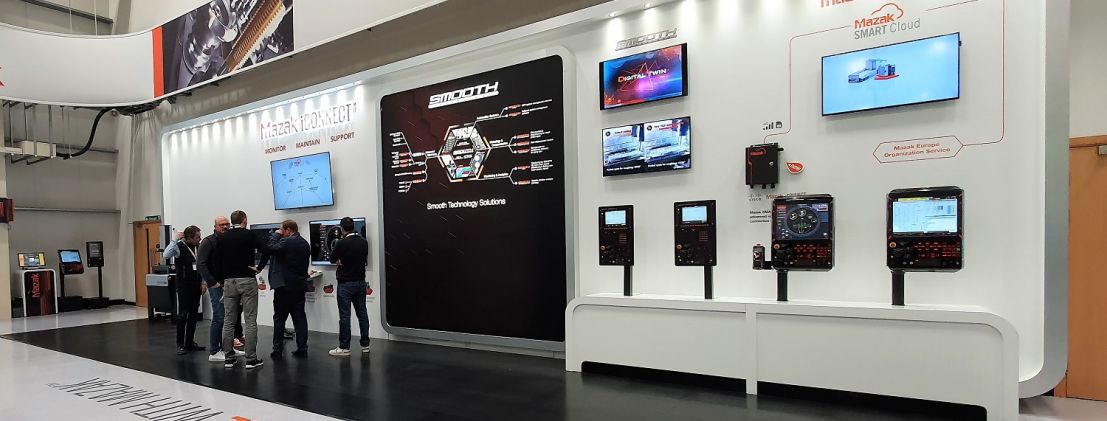
Note: This article was translated using Ai-translation.