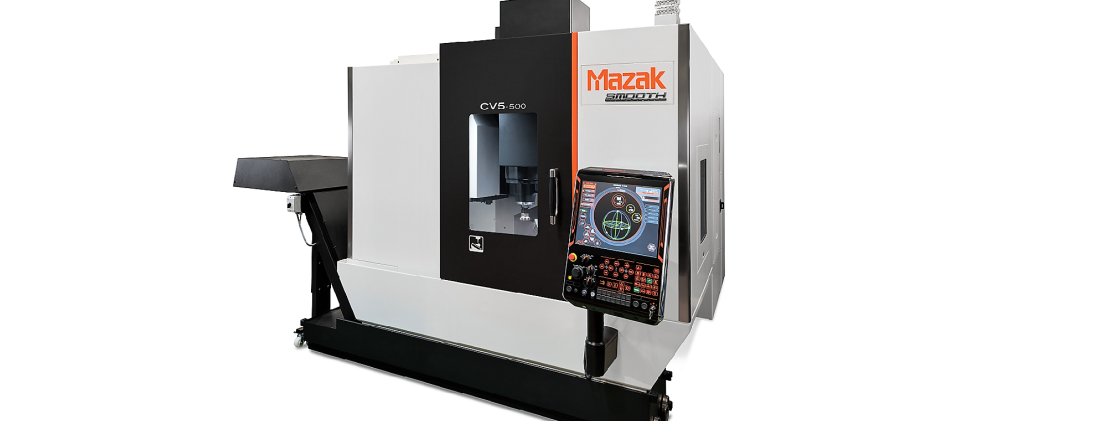
Automating the Mazak CV5-500 5-axis machine
Yamazaki Mazak’s CV5-500, the highly successful 5-axis machining centre built at its European plant in Worcester, is great for automated production with the addition of the new MA-20/400 fully integrated ‘plug-and-play’ part-loading solution. The integrated cell provides a highly affordable and compact automated solution, making it ideal for subcontractors, start-ups and job shops wishing to automate prismatic components in medium to small batch sizes.
The CV5-500 has been designed for easy integration with automation with access for robot loading positioned at the side of the machine, providing operators with unimpaired accessibility to the working area. The highly versatile 5-axis machine, with a 500 mm diameter table, is unique in its category due to its high-rigidity bridge construction with a fully supported trunnion table that travels in the Y-axis direction under the bridge, ultimately delivering a highly accurate and extremely compact machining solution. With rapid traverse rates of 36 m/min in the X-, Y- and Z-axes, the machine delivers agile performance that is boosted by an optional 18,000 rpm 18.5 kW high-speed spindle, which includes core cooling through the X-, Y- and Z-axes ballscrews, all backed up by Mazak’s comprehensive Thermal Shield by to ensure stable machining accuracy.
Lights-out operation
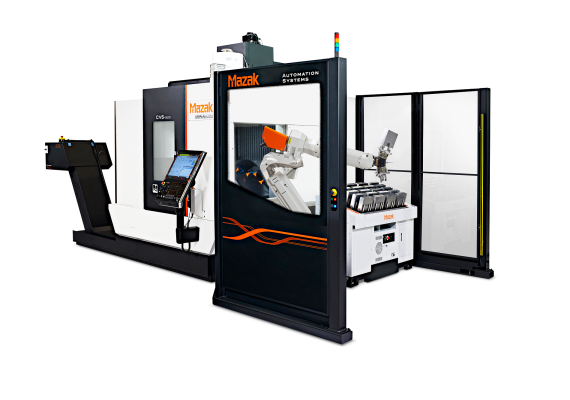
The major benefit of the MA robot solution is the ability to increase production on demand through lights-out operation, without the burden of adding additional labour. Highly skilled operators are thus freed-up to perform more valuable tasks, such as programming and setting, while the automation takes care of the repetitive loading and unloading tasks. The cell also offers the potential to extend the productive hours of the machine with unmanned and lights-out running either overnight or at weekends. No specialist knowledge for either programming or setup is required for the MA, which results in a very short learning curve for operators. With the GUI embedded seamlessly into the SmoothX CNC, operating the robot is exceptionally intuitive with as little as five minutes is required to set-up and change-over workpieces. Raw material and finished components are exchanged to and from the machine by a 20kg payload robot with a double gripper hand for simultaneous load and unload to minimise the non-cutting time. Additionally, the MA provides safe unobstructed access to the robot area thanks to a fully CE-compliant fenceless security system operated by a light curtain.