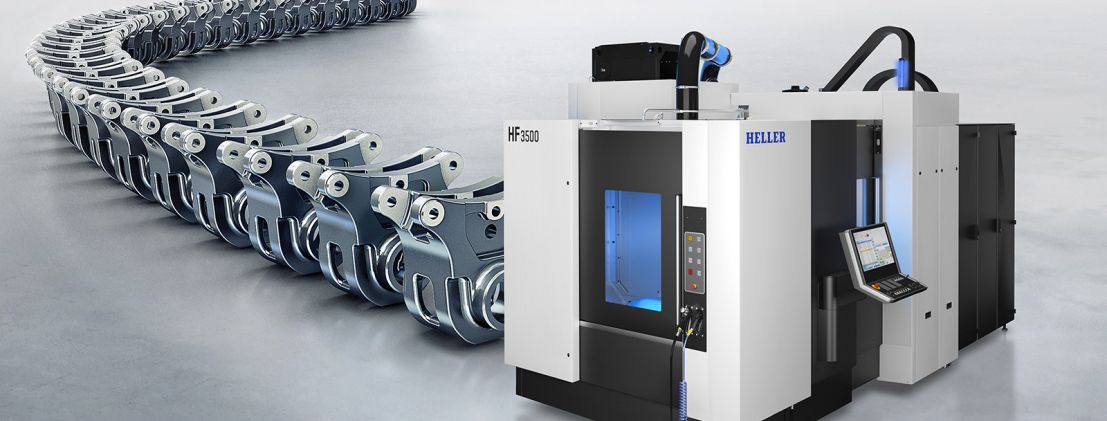
HELLER launched new generation of the 5-axis machining centre HF
With the brand-new virtual event format V-CON 2020 in November, HELLER launched its new generation of the 5-axis machining centre HF. HELLER first presented the 5-axis machining centres from the HF series with the fifth axis provided by the workpiece in 2016. Providing powerful dynamics and significantly reduced idle times and the unique selling proposition of AB kinematics in combination with the counter bearing, the series has been proven in practice for years now.
HELLER sees the application of the series’ first generation – usually ordered with pallet changer – primarily for medium batch sizes in series production and for productive machining. For the second generation, HELLER has now expanded the machines’ range of applications. The goal is to provide greater universality, including single-part manufacturing, combined with the HELLER genes of productivity, precision and reliability. Among the most significant changes on the second generation are the new machining units providing even higher performance and the optional use of a second drive in the Z-axis.
New spindle units
A key component of the second generation of the HF series are the new machining units. The goal was to combine the benefits of the HSM spindles already known from the H series with the advantages of a motor spindle. The machining trials carried out so far and the technical data show that this has been achieved. The second generation of the HF series comes equipped with the newly developed HELLER Spindle Units (HSU) in in-line design. These spindles are "made by HELLER" and produced on the company’s own high-precision manufacturing line. HSU spindles are set to zero dimension, allowing quick and cost-effective replacement of the zero spindle if service is required, providing low Total Cost of Ownership (TCO) for the customer. Compared to the previous motor spindles, the HSU spindles are also more robust and powerful in terms of their machining behaviour.
The new Power Cutting (PC) machining unit, for example, provides 12,000 rpm speed and 228 Nm torque in combination with an HSK-A 63 tool interface. The Speed Cutting (SC) version allows speeds of up to 18,000 rpm and 103 Nm torque combined with a short run-up time. The two DynamicCutting (DC) machining units are brand-new. The HSK-A 63 DC spindle has been specifically designed for a different workpiece spectrum, for increased universality and flexibility and provides speeds of up to 16,000 rpm combined with a high torque of 180 Nm whilst enabling up to 400 Nm in combination with an HSK-A 100 tool interface. Another important factor in practical application or series production are the run-up times causing non-productive times. In this regard, HELLER has succeeded in achieving a massive reduction with the new machining units. Moreover, the different available versions Power, Speed and now PRO, for the second generation, provide the optimal choice for each application at hand.
New additional functions
The first generation of the HF series already provided extremely high milling stability and precision, also due to the counter bearing at the swivel rotary table. With the PRO equipment variant, the second generation of the HF series also offers a classic gantry drive in the table axis (Z) with two physically separated axes in the control and two direct measuring systems. A major advantage resulting from the extra rigidity in the table axis is the ability to absorb maximum process forces in Z direction. This is a useful option, e.g. in combination with the high-torque DC machining units, or if the machining centre is to be used for more universal applications, for example for single-part manufacturing with maximum 5-axis precision and contour accuracy or, if it is planned to equip the machining centre with a turning function, using a high-speed rotary torque table. In addition to the gantry drive, the new HF series will come with further new functions at the launch, including the HELLER out-facing head system. An additional machine axis (U) integrated into the machine control allows easy and highly productive turning of complex inner and outer contours.
Productivity for universal and flexible applications
In addition to the benefits the new generation offers for series production, it also provides measurable advantages when used for single part manufacturing. In total, the new generation HF series will not only provide higher productivity and robust precision through its universal and flexible use but will also significantly expand the spectrum of potential buyers, especially as reliability and robustness have
been increased through numerous optimisations and through increased rigidity of key components and shortening the distance from the spindle front edge to the rotary centre of the B-axis. Moreover, a design for table loading available in the future will make it possible to automate this series in an optimal way.