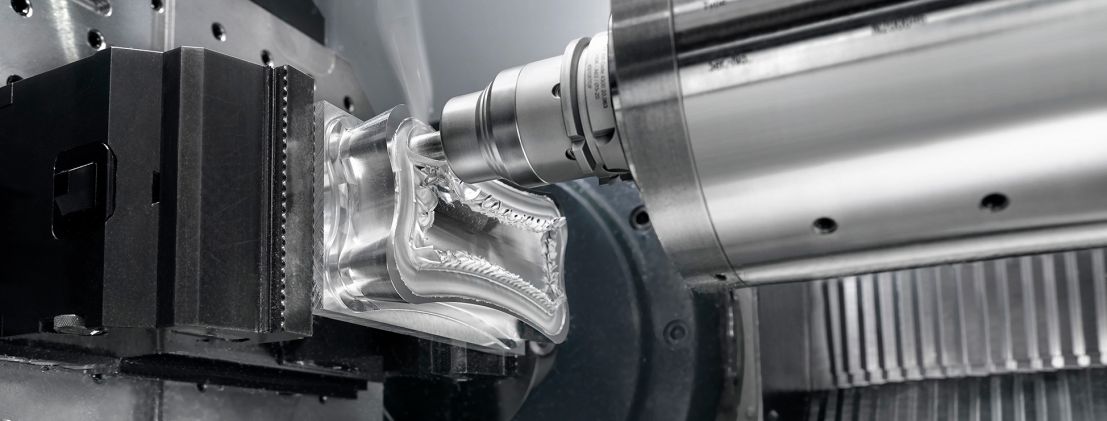
HELLER enables Friction Stir Welding on all Machine Series
Known as a green joining technology for non-ferrous metals such as aluminium, friction stir welding (FSW) has established itself in a number of industries. In future, manufacturing companies using HELLER machines will no longer need any additional hardware for this technology. Instead, they will be able to perform this process in a single setup on all their innovative 4-axis or 5-axis machining centres.
Friction stir welding is a good choice when it comes to producing high-quality cavity-free and tight welded joints with excellent fatigue properties. Accordingly, this process is often applied in the manufacture of reservoirs, tanks and containers as well as in shipbuilding and aerospace engineering. In addition, this joining technology is increasingly establishing itself in the electrical industry and in automotive engineering with the growth market of e-mobility – for example, for the welding of battery housings. According to HELLER Managing Director Dieter Drechsler, it provides several advantages for all areas of application.
Firstly, the quality produced is very high. Due to the comparatively low heat input, a very fine-grained structure without cracks or pores is created in the material. Distortion in the component is minimal. As a result, the welded seam meets the highest standards in terms of tightness and crash behaviour.
Secondly, it offers many key advantages with regard to environmental and health aspects, which is why friction stir welding is also referred to as a green technology. The reasons for this are: compared to conventional welding methods, no dangerous light flashes or hazardous fumes that would have to be extracted are produced during the joining process. Moreover, the environmental balance of the process is very favourable because of the low energy consumption.
Thirdly, the high cost-effectiveness is a real profit driver. As no consumables such as cored wire or shielding gas are required, consumption costs are minimal.
Eliminate additional work steps
The welding process becomes a particularly interesting technology with the successful integration into modern HELLER machine tools. It allows users to eliminate an additional work step and only requires the inexpensive tools, activation of the HELLER technology cycle and the ‘adaptive control function’ in the Sinumerik 840D sl control.
The machine operator can easily program the welding path at the CNC control panel using G-code. The transfer of CAD/CAM data is also possible without any problems. In order to start the welding process, it is also necessary to determine the key parameters of pressure and speed. These depend, among other things, on factors such as the material composition and the required type and depth of the weld seam. According to Dieter Drechsler, this task poses a certain challenge. However, “our experienced experts are of course there to support you if you wish. And initial pilot projects have shown that our customers’ machine operators are able to very quickly manage this task on their own.”
Once determined, pressure and speed can be called up via a cycle. After the welding process has started, the Siemens CNC logs the entire workflow and reliably controls compliance with all parameters. Previously required ‘load cells’ are obsolete.
At the same time, the variety of joint types that can be produced is quite large. In addition to classic butt joints, corner and T-joints are also possible. Even lap joints – single, multiple and as a T-variant – can be realised without any problems.
How does friction stir welding work?
During friction stir welding, the pin-shaped rotating tool is plunged into the gap between the components to be joined with high axial force until the so-called tool shoulder rests against the surface of the component. The friction created during this process heats up and eventually plasticises the component material. As a result, the materials of the components mix and form a bond in the joint gap. Now the tool, which continues to rotate, is moved along the joint gap with constant contact pressure, while the material is steadily plasticised and mixes around the tool pin. As a result, a high-quality weld seam is created. At the end of the weld seam produced, the feed motion is stopped and the tool is lifted out of the joining zone.