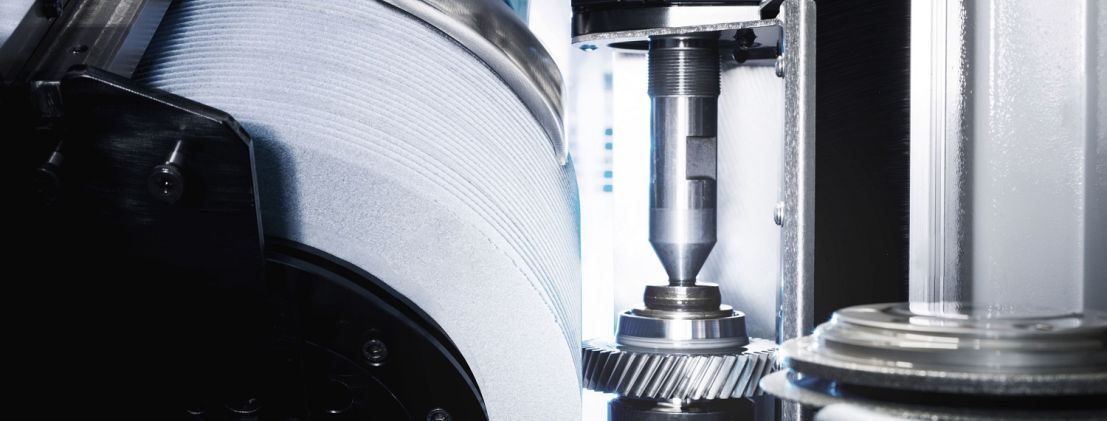
Grinding Solutions EMAG SU deliver Extreme Surface Finish for E-Mobility
The automotive engineering industry has always prioritized precision and reliability. However, with the advent of e-mobility, these demands have once again increased. E-motor components require even greater levels of perfection, particularly in terms of surface finish, to avoid any loud noises in the gear components. EMAG SU has emerged as a leading technology in this field, attracting the attention of production planners. Their high-performance solutions for gear grinding have shown impressive results, with features such as short chip-to-chip times, intelligent axis concepts, thermal and mechanical stability, and user-friendliness. This article will delve into the specific machines and processes that EMAG SU focuses on.
Outstanding solutions for the field of gear profile grinding include the G 250 machine on the one hand and the G 160 on the other. The G 160 is used for components up to module three and with a maximum O/D (Outer Diameter) of 160 mm. In this field of application, it is the fastest machine on the market, which is made possible by two parallel workpiece tables that move alternately at high speed to the grinding wheel. Thus, while machining one component, the internal loading robot inserts a blank into the other spindle or unloads the finished component beforehand. In addition, the axis concept ensures perfect surfaces, which are so important in e-mobility. The decisive factor here is that the G 160 does not have a tangential axis, but instead, the existing Y and Z axes generate a "virtual" tangential axis through simultaneous movement. As a result, the distance between the A axis and the tool contact point is minimal, which in turn prevents the so-called "ghost frequencies" on the surface of the component. The possibilities this approach opens up for e-mobility are shown, for example, by the example of an "intermediate shaft" with 21 teeth and a normal module, where a floor-to-floor time of only 33 seconds (including entanglement compensation and proportional dressing time) and a grinding time of only 25 seconds are achieved. Similar performance values are shown for an input shaft with 26 teeth and a module of 1.6 mm. Here, the pure grinding time is only 28 seconds.
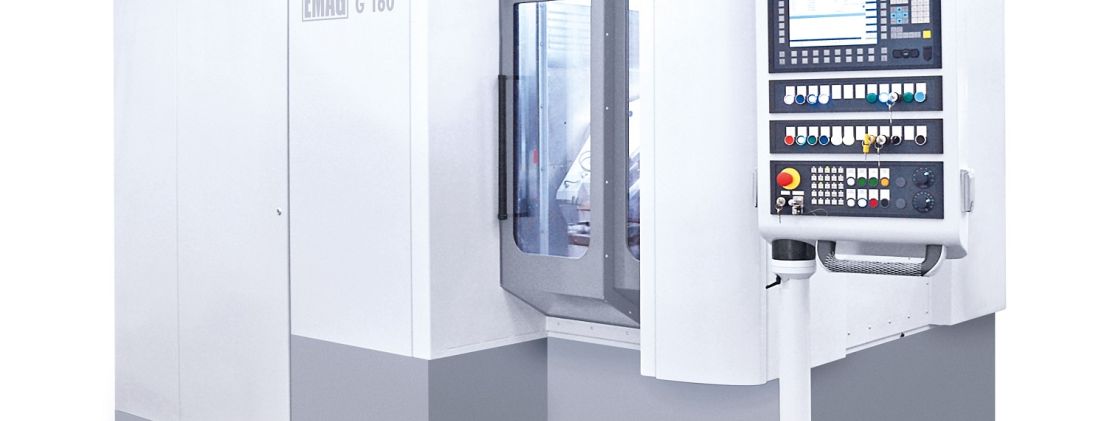
Minimum floor-to-floor times
The larger G 250 machine also scores with precision, minimum chip-to-chip times, short setup times and reliability for components with a maximum length of 550 mm. The machine also has a double table (like the G 160). Loading and unloading operations as well as component measurement are thus performed in cycle time-concurrently. Additionally, the grinding mandrel can accommodate grinding wheels with different diameters, and the entire design is very rigid. Gear-generating grinding and profile grinding takes place on the main grinding spindle, so the machine does not have thermal growth. It can also be retooled for the other process in just a few minutes. In the field of e-mobility, for example, this approach is used for grinding axle drive wheels. The floor-to-floor time here is only 69 seconds (including entanglement compensation and proportional dressing time), with the actual grinding time even comprising only 58 seconds. The G 250 achieves a comparably high productivity level when machining pinions with a strong crowning in the tooth flank profile and normal crowning in the flank line. The bottom-to-bottom time is 33 and the grinding-only time is 28 seconds. A DIN 3962 quality of 4 is achieved.
Future of gear grinding
Furthermore, EMAG SU illustrates what the general future of gear grinding could look like with the establishment of the new "Sky Grind" process. Here, the final grinding on the gear is carried out completely dry - with great financial advantages for the users, because the filter system, cooler and co. (which are normally required for wet grinding) are no longer needed, thus reducing the initial investment. In addition, energy consumption is massively reduced. The whole thing is made possible by a dual-tool system with two different tool spindles in the machine: one for finish-machining by hobbing and one for finish-machining by grinding. In practice, this means that, for example, in the case of the classic automotive gearwheel with 100 µm allowance per flank, the sky-grind process removes 90 µm by hobbing and only 10 µm by gear-generating grinding. In the end, the cycle times of conventional wet gear grinding and the Sky-Grind process are very similar; however, the costs are very different.
How can EMAG SU's know-how and offering be summarized? "You could certainly say that we guarantee our customers competitive advantages and a fast return in investment," answers Alexander Morhard from EMAG SU. "To this end, we continuously invest in research and development to further increase the efficiency and environmental friendliness of the machines. The result is perfect solutions for the production of ultra-fine surfaces with different contours."