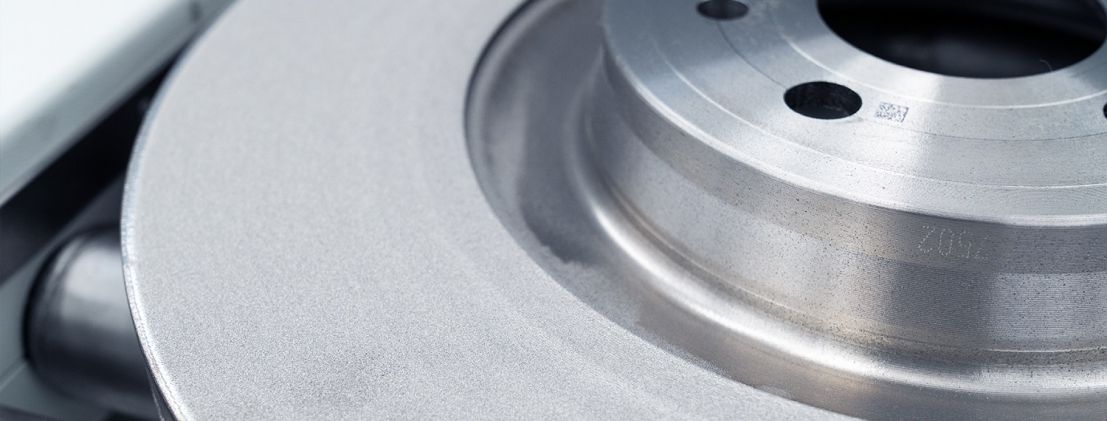
EMAG Laser Deposition Welding for Efficient Brake Disc Coating and EURO 7 Compliance
The EURO 7 standard will bring a major shift to the automotive industry. For the first time, regulations will extend beyond combustion engine emissions to include brake abrasion and other sources of particulate matter. The key takeaway is clear: many existing vehicle models must significantly reduce their particulate emissions. As a result, OEMs and suppliers are searching for innovative braking solutions, with coated brake discs emerging as the leading approach. But how can these coatings be applied reliably and efficiently in high-volume production? EMAG provides the answer: a fully industrialized laser deposition welding system for brake disc coating—already proven in production. But what makes this solution stand out?
The issue is both simple and pressing. According to the EU, traditional braking systems generate excessive particulate matter. The new EURO 7 regulations impose a strict upper limit of just 7 milligrams per kilometer for all new vehicles. In contrast, many current models emit up to 40 milligrams, depending on their design. For manufacturers—especially those producing larger vehicles with higher emissions—this presents a significant engineering challenge. Brake systems are safety-critical components with intricate designs, making modifications complex. The primary concern lies in the two key friction partners: the brake disc and the brake pad. Their interaction is the main source of particulate emissions, driving the need for a more advanced coating solution.
A Technical Challenge
What are the options for reducing brake particulate emissions? This question has long occupied developers, but many proposed solutions have proven impractical. For instance, extraction systems positioned near the brakes capture only a fraction of emissions while adding complexity, requiring additional installation space, and increasing unsprung mass. Similarly, NAO (Non-Asbestos Organic) brake pads offer only a temporary reduction in emissions—once the brake discs wear slightly, particulate levels quickly return to their original values. In this context, hard-coated brake discs are emerging as the most effective solution. By applying a protective layer, conventional brake discs gain improved resistance to corrosion, wear, and fine dust generation. While hard-coated brake discs are not a new concept, their use has been limited to niche applications due to high production costs. Traditional methods like thermal spraying and electroplating lack a metallurgical bond with the base material, requiring complex pre-processing to ensure adhesion. These coatings are also often too thick, and the application process generates excessive heat. EMAG’s latest development in laser deposition welding marks a breakthrough in this field. This innovative process enables cost-effective, high-volume production while ensuring a strong bond between the coating and the brake disc. Additionally, it offers flexibility in material selection, making it a reliable and scalable solution for the next generation of brake systems.
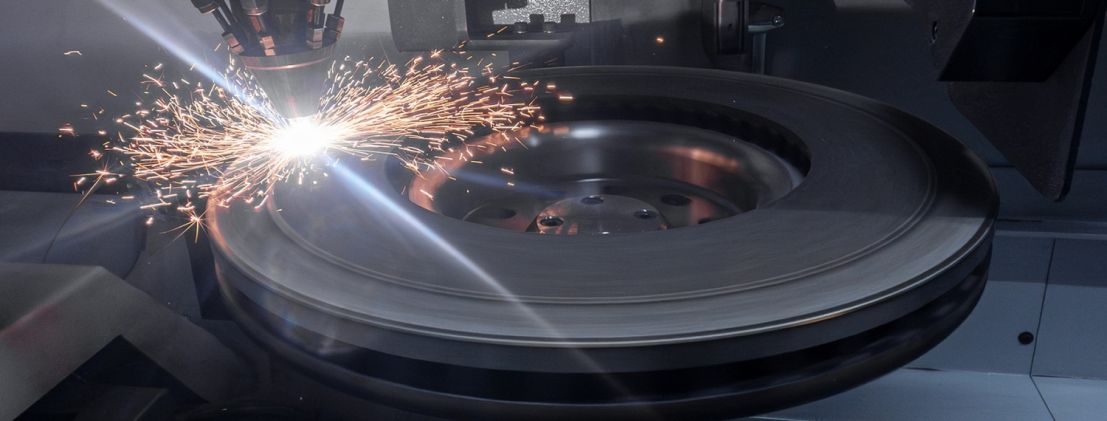
ELC 450 LM for laser metal deposition
The ELC 450 LMD is an innovative machine solution from EMAG that is characterized by its modularity and flexibility. The basic idea behind the ELC 450 LMD is the use of process modules that can be combined and expanded according to customer requirements. The machine is available in various configurations depending on the number of process modules. The basic version, the ELC 450 LMD, has one process module. The ELC 450 DUO LMD is equipped with two process modules, while the ELC 450 TRIO LMD, as the name suggests, uses three process modules. These modular machine concepts make it possible to optimally meet customer requirements in terms of shift structure and productivity. This then determines the choice of machine configuration. The ELC 450 LMD can realize both 1-shift and 2-shift systems. The combination of laser power and application rate determines the most suitable machine concept for the respective application.
The longer service life of coated brake discs also has a positive effect and helps to reduce the environmental impact. In contrast to conventional brake discs, coated brake discs have a significantly longer service life, which means that they need to be replaced less often. This reduces the need for new brake discs and helps to reduce the environmental impact of their manufacture, transportation and disposal. In addition, the new generation of brake discs reduces vehicle maintenance, saving time and money. Overall, the coating of brake discs offers a sustainable solution for extending the service life of brake discs and reducing the environmental impact.