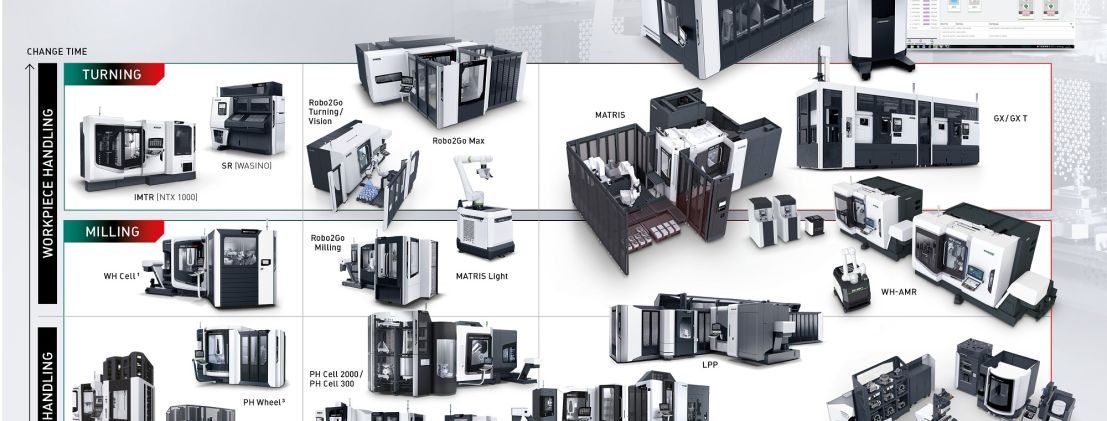
DMG MORI's automation portfolio is growing rapidly
Flexible automation of production processes is high on the agenda of an increasing number of companies. The quest for productivity and efficiency in order to remain competitive on the global market is driving this development. After all, the better the utilization of a production facility, the better its economic as well as ecological balance. DMG MORI has been shaping this development towards increasingly autonomous processes for many years with innovative automation solutions. The portfolio now comprises 57 automation solutions in 13 product lines for workpiece or pallet handling – including the complete hardware and software. In addition, there are the PH-AGV and WH-AMR driverless transport systems. DMG MORI can thus equip and in many cases retrofit 150 different machine models.
Central Tool Storage for up to 1,440 tools
The wheel magazine developed by DMG MORI, which has been sold over 1,600 times, offers fast provisioning times, a compact design and operates absolutely reliably. Based on this technology, the machine tool manufacturer has developed the CTS (Central Tool Storage), a central tool magazine. Thanks to a footprint of just 29 m², it can be installed in a space-saving manner at any location in production. There, with space for up to 1,440 (ISO 40) or 960 (ISO 50) tools, it functions as the basis for an automated tool supply system, which DMG MORI will demonstrate in Pfronten using a transport shuttle. The modular tool magazine has a compact design and can also be expanded in stages by 360 (ISO 40) or 240 (ISO 50) tools. At full capacity, the CTS measures 6,500 x 4,450 mm.

Automation for 5-axis universal machining
DMG MORI developed the PH Cell series to provide users with flexible pallet handling with different pallet sizes. Both the PH Cell 300 and PH Cell 2000 can be equipped with a different number of pallet spaces and different pallet sizes thanks to their modular racks. Both systems are also quick to install and easy to operate.
The latest member of the series is the PH Cell Twin, which enables DMG MORI to automate two machining centers. Up to 30 pallets of size 320 x 320 mm can be accommodated here. For larger pallets of 400 x 400 mm or 500 x 500 mm, there are 24 and 18 pallet spaces, respectively. At the in-house exhibition, the PH Cell Twin automates production on a DMU 75 monoBLOCK 2nd Generation and a DMU 50 3rd Generation.
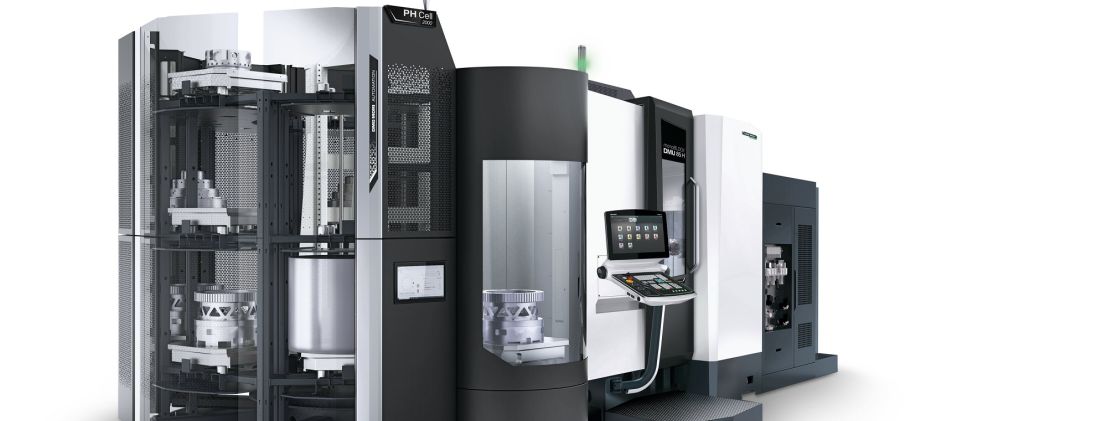
Flexible robot automation
The Robo2Go family allows flexible robot automation for flexible handling of workpieces that are either placed in a magazine or directly on a pallet. In addition to Robo2Go Turning and Robo2Go Max for turning centers, the range also includes Robo2Go Milling for machining centers. All models ensure safe operation without protective fences. Lasers scan the environment and slow down or stop robots as soon as a human enters the work zone.
DMG MORI is demonstrating all three variants in Pfronten: Robo2Go Turning is installed on a CTX beta 1250 TC. On a CTX gamma 2000 TC, the Robo2Go Max will clamp and unclamp larger workpieces. The Robo2Go Milling is on display in combination with a DMU 40 eVo.
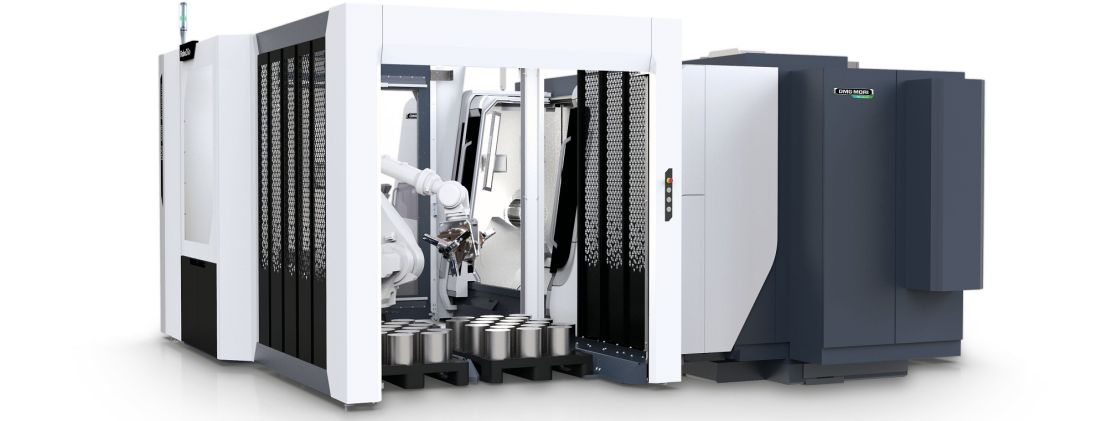
Automation goes digital
The future of industrial manufacturing technology will be determined by the quality of the interdisciplinary interaction of mechatronics, automation technology, and information and communication technology. In this context, DMG MORI is positioning the CELL CONTROLLER LPS 4. The new master computer is capable of integrating not only all individual machines, but also manufacturing cells and manufacturing systems on the store floor to form a flexible manufacturing network. If necessary, the new development also controls the automatic supply of materials, tools and operating supplies via autonomous transport vehicles. This gives the vision of the digital store floor greater contour and clarity.
The Cell Controller LPS 4 combines everything from pallet handling and workpiece handling to the control of AGVs in one – thanks to DMG MORI Connectivity with direct interfaces to ERP and MES or APS systems as well as into tool management. The necessary interoperable connection of the CELL CONTROLLER LPS 4 to higher-level planning and control systems at the production and company level takes place via corresponding interfaces, e.g. for ERP or MES, and a central data hub in which the data or data sets are collected, provided and exchanged.