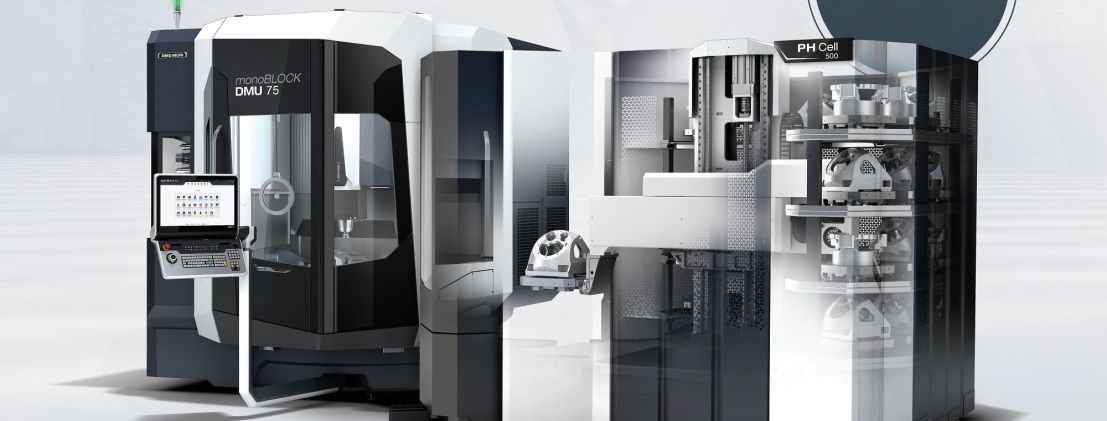
DMG MORI PH Cell 500: Modular Pallet Handling with Up to 500 kg Transfer Weight
With the PH Cell 500, DMG MORI is expanding its series of modular pallet handling systems with a compact model for transfer weights of up to 500 kg. It is compatible with the DMU 65 and DMU 75 monoBLOCK 2nd Generation as well as the DMU 65 H monoBLOCK. Depending on the configuration of the rack modules, the PH Cell 500 offers space for up to 32 pallets. The maximum workpiece dimensions are 500 x 500 x 750 mm. The transfer weight is 500 kg. Like the other models in the series, the PH Cell 500 is ergonomic and easy to operate thanks to the Pallet Master software.
“With the consistent further development of its pallet handling systems, DMG MORI is underlining the high importance of automation as a fixed pillar in the Machining Transformation,” says Cornelius Nöß, Managing Director of DECKEL MAHO Pfronten, explaining the focus on products such as the PH Cell 500. The new pallet automation enables highly flexible automated production of small batch sizes and individual parts. The reason for this is the modularity of the system, which enables customized configuration. In practice, the PH Cell 500 can increase spindle hours by up to 300% and reduce unit costs by 50%.
The PH Cell 500 is supplied with one storage module as standard. Equipped with three shelves, it offers space for twelve 400 x 400 mm or nine 500 x 500 mm pallets. The version with four shelves has space for 16 of the smaller or twelve of the larger pallets. A combination of different pallet sizes is also possible. The PH Cell can be retrofitted if the machine is equipped with automation preparation. The same applies to the extension of the pallet handling system with a second rack module. DMG MORI thus guarantees a needs-based configuration that meets the production requirements at any time – even retrospectively.
Reliability and ergonomic operation
Like the PH Cell 800, DMG MORI has also designed the PH Cell 500 to be stable. As steel pallets are also used here, the integrated clamping cone system in the machine table is utilized. This means that no zero-point clamping station is required on the machine table and at the same time the chip fall is better. Ergonomic operation is ensured by the rotating set-up station as standard and the separate operation of the Pallet Master software via touchscreen.