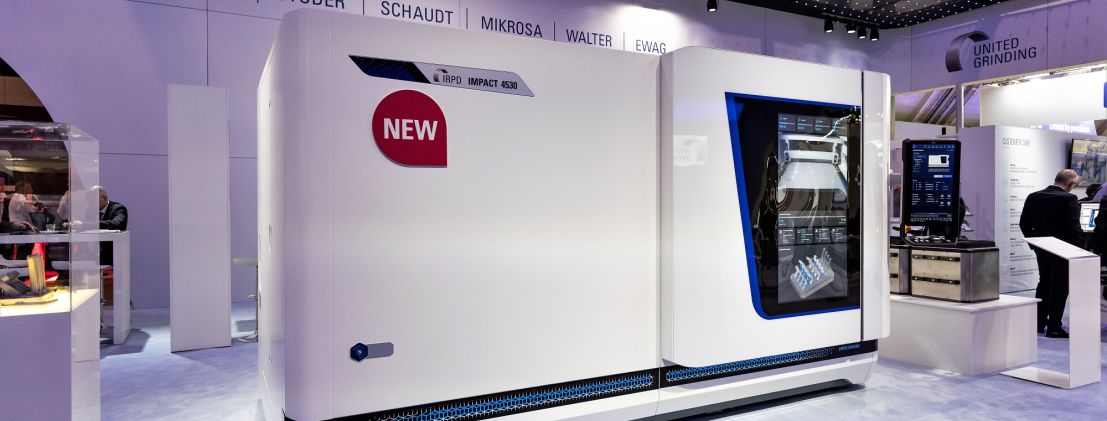
United Grinding launches IMPACT 4530 3D metal printer
The United Grinding Group enters the world of Additive Manufacturing with the new IMPACT 4530 3D metal printer. The new metal printer from IRPD produces high-quality metal workpieces on a modular and scalable basis, for the classic job shop, the aviation industry, automotive engineering industry, the energy sector, medical technology, tool production and automation. Thanks to C.O.R.E., the UNITED GRINDING Group’s hardware and software architecture, and Industry 5.0 standard, customers using this machine are optimally prepared for the challenges of the future.
“Additive manufacturing is a transformative technology and it will play an increasingly important role for any industry. As an AM machine tool for industrial use, the IMPACT 4530 is therefore pioneering”, says Stephan Nell, CEO of the United Grinding Group. The ma-chine produces metal components by selectively melting metal powder using the LPBF process (Laser Powder Bed Fusion). For this purpose, it is equipped with industrial fiber lasers (two or four, depending on the configuration) each providing 1000 watts of laser power. The micro welding process takes place in the tempered machine core, which delivers uncompromising quality, production stability and reproducibility of components. The heart is the vacuum-capable process chamber, a robust cast component with the highest rigidity, which is hermetically sealed off by the exchangeable build and powder storage containers.
Separate operating and loading area
The innovative system design is the foundation for the machine’s high productivity and safety: In order to ensure powder contamination-free operation, the IMPACT 4530 has separated operation and loading areas. Within the machine, an automated changing system handles the loading and unloading of the gas-tight containers holding metal powder, build plate and parts. Furthermore, this enables short processing times (job to job in 15 minutes) and quick and clean material changes. Cleaning and maintenance of the system, which is accessible from three sides, is also simple and straightforward, thanks to the special coating of the chamber interior.
As a new machine tool from the United Grinding Group, the IMPACT 4530 comes with C.O.R.E., the cross-brand hardware and software architecture, including a 24" multi-touch operating panel. The system is easy and intuitive to operate, and it supports operators with smart software and can efficiently network with other machine tools. Thanks to the processing power of C.O.R.E., the IMPACT 4530 can, to a large extent, be prepared for production autonomously. Furthermore, job-specific programming or setup at the machine is not required.
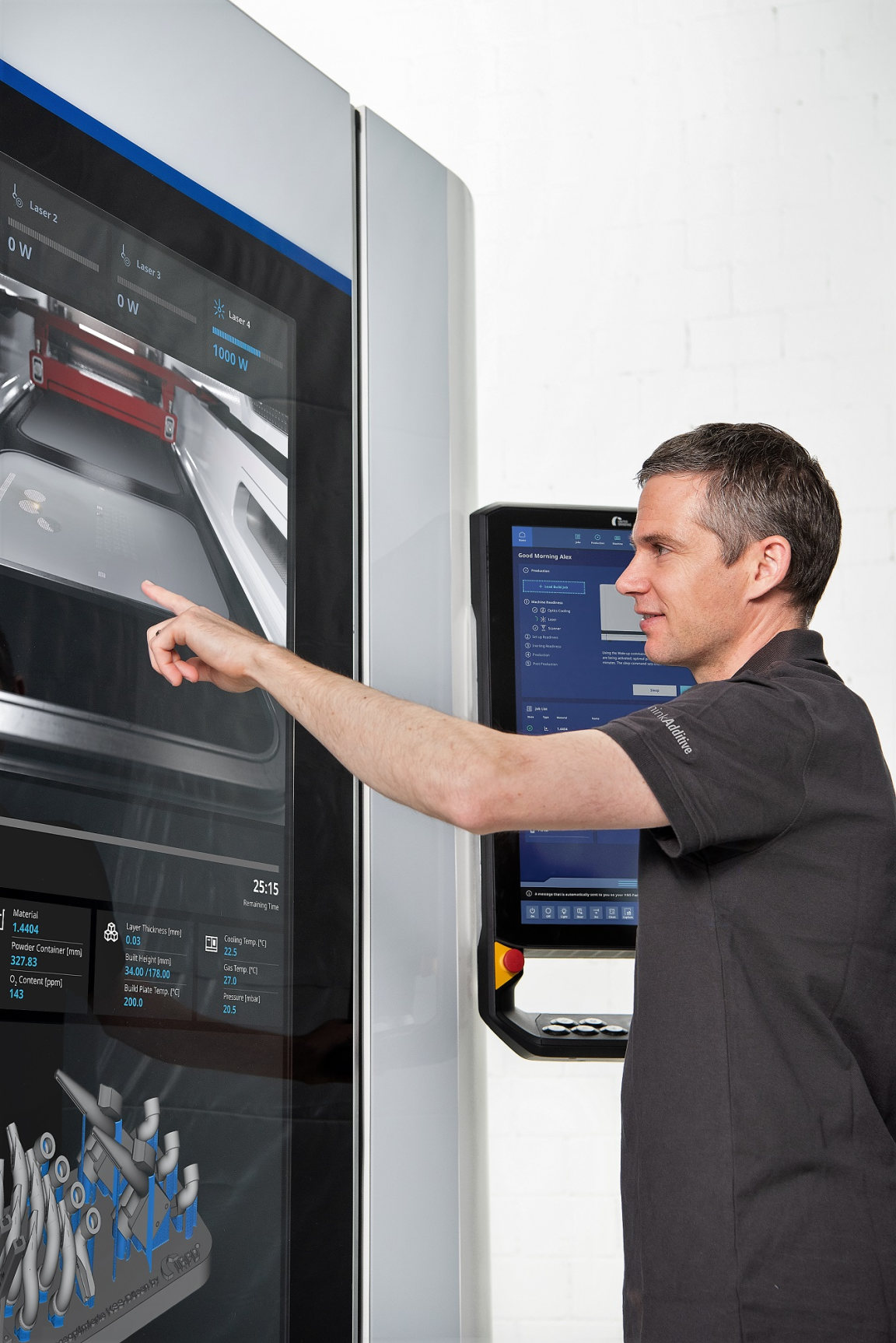
High autonomy thanks to state-of-the-art technology
The build jobs are created on a CAD-CAM workstation and are sent to the machine as a print job, containing all process-relevant data. The machine is ready for use after just a few minutes. Using the internal camera, a view of the process – including sensor data and ma-chine measured values– is transferred live to a large 54" display embedded into the machine face door. Hereby, a detailed overview of the build progress is available at all times. The process is facilitated by premium scanner and sensor technology, which record process emissions from the melting area in detail and help maintain the lasers’ alignment within micrometers even during long build jobs. The application area of the system ranges from stand-alone all the way up to a highly automated network of several machines.
AM is a technology that, compared to most conventional manufacturing processes, enables the production of lighter and functionally integrated components and systems. “The IMPACT 4530 can work with all standard metals and, with its stable production conditions, precision, quality and scalability, it is the world's first AM machine tool for industrial use ‘Made in Switzerland’”, says Daniel Erni, Managing Director of IRPD. The company based in St. Gallen belongs to the United Grinding Group and is one of the market and technology leaders in Additive Manufacturing in Switzerland.
Advantages at a glance
- High system autonomy: scalable use from stand-alone machine to integration into a fully-automated system network
- Separate operation and loading areas with automatic changing system and gas-tight containers enables machine operation without contact to metal powder
- Short processing times between printing process (job to job in 15 minutes)
- Tempered machine core for precise cooling of critical optics, electronics and mechanical parts
- Two or four optimally synchronized laser beams with 1000 watts of power each
- Ultra-modern sensors and 3D scanner technology enable process monitoring
- C.O.R.E. hardware and software architecture including 24" Full HD Multi-Touch display
- Data-supported virtual view of the process inside the machine, thanks to an internal camera and 54" display
- Easy maintenance and cleaning thanks to good accessibility and special coating
- Precise measurement and control of protective gas with up to ten sensors
- Reduction of soot deposits through targeted protective gas flow
- Industry 5.0 standard