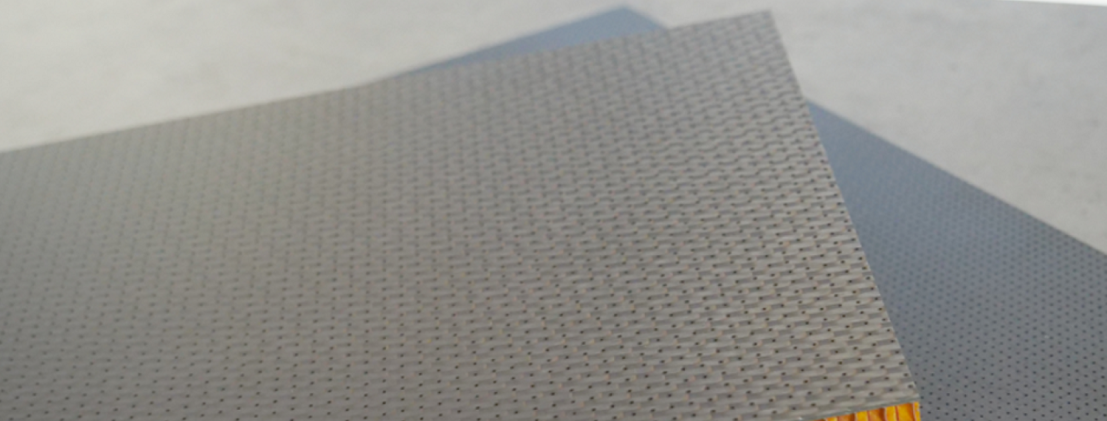
LZH Develops Process for Laser Drilling CFRP
LZH scientists have developed an automated process for laser drilling that facilitates the machining of carbon fiber-reinforced plastics (CFRP). This is particularly interesting for lightweight construction and sound insulation.
Composite materials such as carbon fiber-reinforced plastics (CFRP) are excellent for lightweight construction and are used, among other things, in automotive and aircraft construction. To simplify the machining of CFRP and sandwich materials, scientists from LZH, together with INVENT GmbH and KMS Technology Center GmbH, have developed an innovative process with an associated system setup.
Simultaneous drilling with small diameters
In this process, a laser beam is split into partial beams by specially designed diffractive optical elements, so it hits multiple locations on the material and generates multiple bores simultaneously. Ideally, this can be done with up to 25 partial beams, reducing the drilling time to only a 25th of the original time, resulting in less than a tenth of a second per bore – a value that cannot be achieved with conventional methods even for larger bores.
With this process, the scientists were able to create bores with diameters ranging from only 1.2 mm to 0.25 mm. This makes them smaller than bores that can currently be implemented with conventional mechanical methods in sandwich and CFRP materials. The use of optomechanics manufactured by KMS Technology Center GmbH also enables high flexibility in bore diameter and pattern without the need for tool changes.
Sound insulation in lightweight construction
Micro-drilling with lasers is particularly interesting in aviation. To reduce aircraft noise emissions, sound-absorbing cladding elements are used to line engines, for example. Such components are often made of CFRP or CFRP sandwich materials and then provided with many small bores over a large area.
Micro-drilling with lasers is particularly suitable for this so-called acoustic drilling because laser drilling is contactless and therefore force- and wear-free. This eliminates high costs due to tool wear and quality problems due to dull drills. In acoustic tests, project partner INVENT GmbH evaluated the sound-damping properties of the laser-drilled sandwich panels as very good.
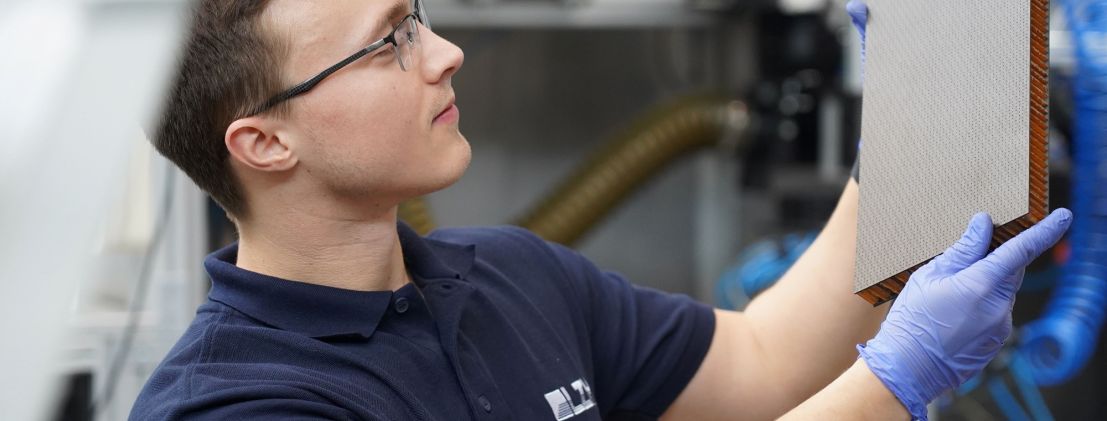