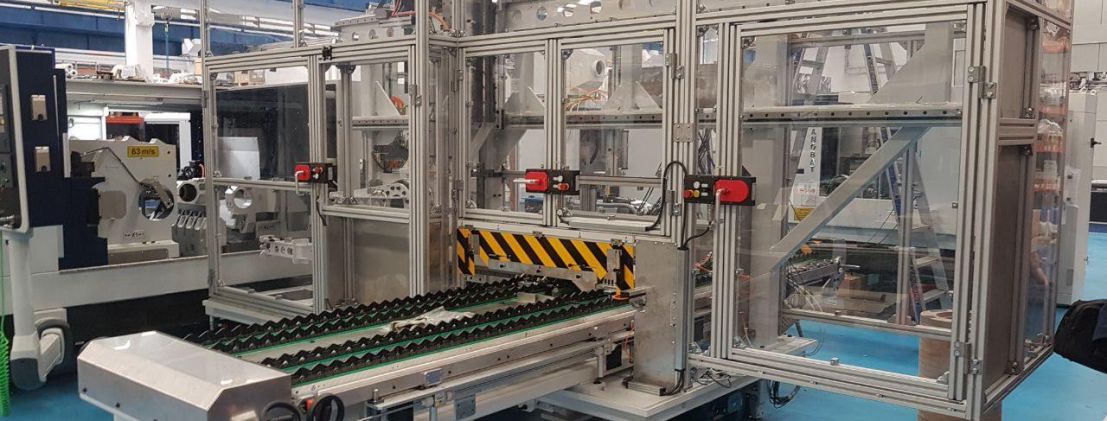
Human-Robot Collaboration could soon be setting the pace in Grinding Factories
Incorporating manual grinding, polishing or brushing processes into automated production might sound good on paper, but it is very difficult to achieve in practice. More and more machine manufacturers are responding to this challenge by offering grinding technology combined with flexible automation systems. Unlike many OEMs, however, SME users are likely to prefer an incremental approach involving moderate individual investments. Existing machines and retrofits can play a special role here. Exhibitors at GrindingHub, the industry meeting point for grinding technology in Stuttgart, will provide insight into their solutions and research projects before the trade fair begins.
One thing is clear: Automation is certainly enjoying a boom. According to the VDW (German Machine Tool Builders' Association), the pressure to raise productivity and the shortage of skilled workers are making it more important than ever to invest in production technology, regardless of the short-term economic prospects. Grinding is no exception here – on the contrary: faster production speeds, more exacting tolerances, reproducible quality and potential savings represent attractive propositions, also for companies that are still offering manual processing.
Concentrated expertise and comprehensive support
Trade fairs such as GrindingHub 2024 (14 to 17 May) show how manufacturers of grinding, honing, lapping and polishing machines are adapting to the demands. The solutions on display include machine tools with dedicated robots for loading and discharging workpieces, or additional robot cells for the automatic execution of testing, cleaning, deburring, laser marking and storage processes. Aimed at driving forward the automation of grinding processes, strategic partnerships are often forged between machine and robot suppliers, for example. Such partnerships bring together expertise from the areas of stationary machines and flexible automation (robotics).
When it comes to automating processes, 3M Deutschland from Neuss demonstrates just how many factors need to be taken into account. The specialist in industrial abrasives is cooperating with Schunk, Lauffen/Neckar, a manufacturer of gripping systems and clamping technology. Both are exhibiting at GrindingHub – a platform which provides comprehensive information and advice on this topic. 3M has put its decades of experience in the automation of grinding into its manual designed to help users determine their exact automation requirements when preparing for projects. The manual includes questions on the optical and technical requirements of surface finishes, the sequence of process steps for specific workpieces, on tools and abrasives. As 3M points out, the number of factors to be considered can be "overwhelming". According to experts, this is no doubt the reason why around two-thirds of all companies seeking to automate processes in their factories bring in external consultants or system integrators. Support is also offered by the university and Fraunhofer institutes affiliated with the WGP (German Academic Association for Production Technology). The primary focus of these is on conducting research into new production technologies, and their effective transfer to industrial production.
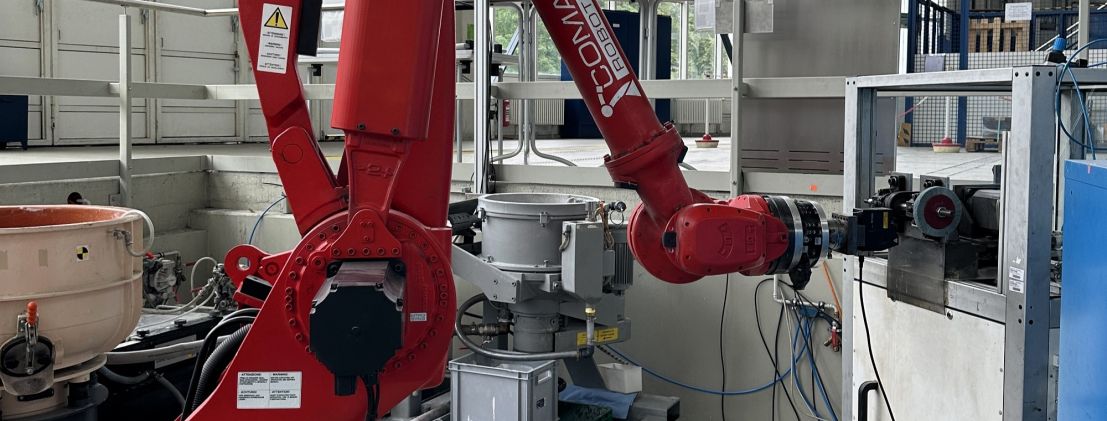
Definition and systematic evaluation of automation goals
"In general, companies are aware of these, or have at least identified certain processes in their production that could be automated. However, many are not sure where to start," says Arturo Bastidas-Cruz, research associate in the Process Automation and Robotics department at the Fraunhofer IPK (Institute for Production Systems and Design Technology) in Berlin. The Institute offers support on precisely this issue. Fraunhofer IPK's analysis of automation potential includes individual consultations and workshops. To this end, Bastidas-Cruz has developed a tool to systematically evaluate the automation potential of production processes. "We have developed a piece of software which formalizes our broad empirical knowledge and allows reliable assessments to be made," he says.
Once a company has contacted the Institute, Bastidas-Cruz visits it to assess the situation on-site and to enter the relevant criteria into the software. The design and sequence of the production process are not the only factors included in the assessment. The required degree of automation is also determined. In some cases, an automation solution which is more flexible than HRC (human-robot collaboration) could represent a better option. Employee safety and the available workspace – crucial factors, especially in smaller factories – must also be taken into account.
The software finally delivers its result in the form of points on a scale: the higher the results are on the scale, the greater the potential for automation. Four out of ten process steps, for example, could have major potential. Different HRC scenarios are compared and evaluated based on the following criteria: transferability, technical risk, approval and cost-effectiveness. The software provides a rough-and-ready overview of the customer's production process. WGP believes that the development of flexible automated systems for assembly and handling is becoming increasingly important due to the trend towards customized production. Human-robot collaboration effectively combines the outstanding cognitive and sensorimotor skills of humans with the precision, speed and mechanical performance of robots. However, the design of these robot systems with their integrated sensors and control technology must ensure that they can be integrated safely into the existing process environment. This raises the question of whether the existing machines offer the right preconditions for such a development.
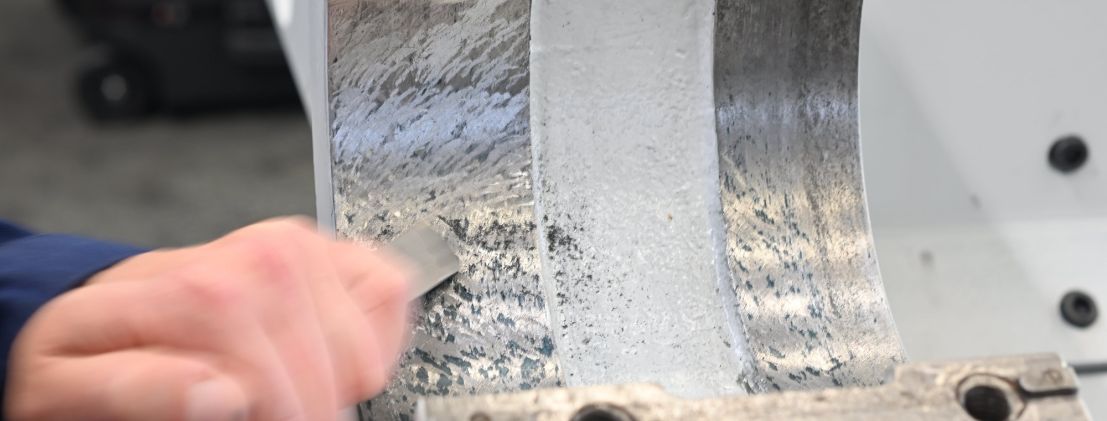
Making existing machines fit for the future
The retrofitting of existing machines in combination with data acquisition and automation is one of the topics being discussed at this year's Schleiftagung grinding conference in Fellbach in Stuttgart, which is a cooperation partner of GrindingHub. Thomas Veit, Managing Director of Automation, Sonder- und Werkzeugmaschinen ASW, is one of the speakers. The company, based in Naumburg/Saale, is a management buy-out of a former Mikrosa plant. Machines were automated in Naumburg and linked lines built there even during the period of the former GDR, says Veit. ASW has enjoyed solid growth from the retrofitting of old Mikrosa machines and the automation of centerless cylindrical grinding machines in general.
The range of automation equipment includes handling systems as well as solutions for the infeed and discharge of workpieces based on conveyor belts, rollers, area gantries and palletizing systems. This also includes modular robot feeders and test cells for quality control. Data acquisition, traceability and the integration of interfaces are key factors in feeding systems, emphasizes Thomas Veit. The software used for the test cells manages the storage of data and evaluates the production monitoring.
When called upon to automate centerless cylindrical grinding machines, ASW is often confronted with series that are ten or 15 years old. "The individual circumstances determine whether the machine still meets its requirements and what measures can be taken to upgrade it," says Veit. When retrofitting a conventional machine to create a fully-fledged CNC grinding machine, the machine first needs to be completely dismantled and then mechanically refitted. This is followed by the conversion of the electrical and control systems. "Following a retrofit, and once equipped with a modern CNC control system, the machine is absolutely on a par with a new machine," emphasizes the expert. The conversion usually costs little more than half the price of a new purchase. The biggest cost factor here is the CNC control system, which could cost a high five-figure sum. The ASW experts therefore have high hopes of securing a joint project with Siemens. This only involves retrofitting the control system, which could reduce the cost of updating a large number of machines. This would benefit small and medium-sized users in particular.
However, the topic of retrofitting has been added to the Schleiftagung agenda not only for technical and economic, but also for sustainability reasons. Conference chair Jannik Röttger notes that extending the service life of a machine whose manufacture has consumed high levels of energy can improve its carbon footprint. The prospect of giving a grinding machine a second life would make it even more valuable in an automated environment.