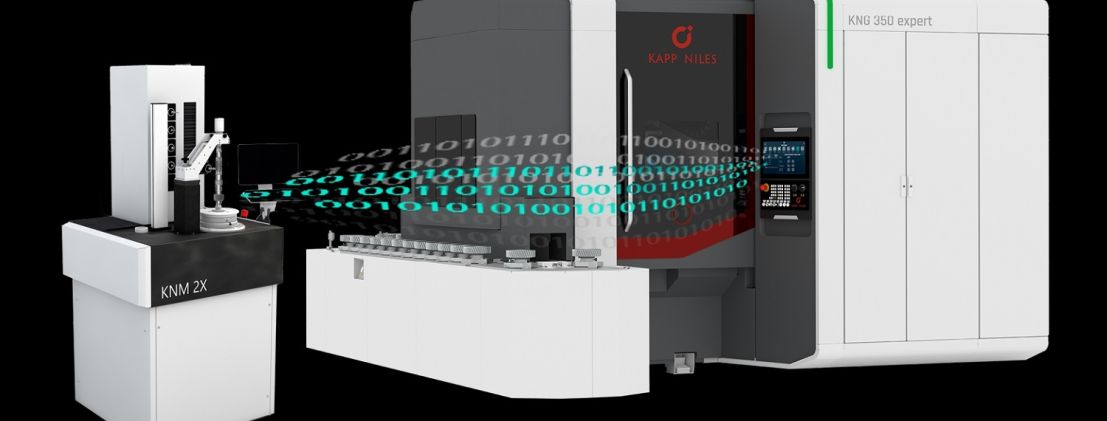
Elevate your digital grinding processes with cutting-edge security solutions
The digitalization of production processes, including those involving grinding technology, holds high expectations. We are approaching the physical limits in terms of grinding machine and tool precision. Accordingly, attention is now shifting towards process optimization and networking in the IoT (Internet of Things) as means of opening up new development potential. Scientists and industrial companies have expressed a common desire to engage in cooperation and networking. However, organizations are keen to retain control over their own data, which is likely to play a decisive role in raising trust levels and acceptance, especially in medium-sized companies.
Process data is a valuable asset. "Awareness levels have risen considerably in recent years," confirms Alexej Voigt, head of Electrical Engineering at grinding machine manufacturer Danobat-Overbeck, Herborn. He gave a talk at the most recent Schleiftagung conference in Stuttgart-Fellbach, held at the end of January. There he discussed the potential of machine data analysis for grinding process optimization and also outlined methods for data acquisition and analysis in digital motor spindles.
Data acquisition – made easy
For Alexej Voigt, using smart components that provide data for real-time monitoring is the key to further optimizing the performance, efficiency and reliability of machines. "They also provide the basis for advanced analytics and predictive maintenance in the form of digital services," says the expert. Nevertheless, he is also aware of the concerns of smaller companies in particular when it comes to retaining control over their own data, and potential cyberattacks. Voigt believes that machine manufacturers have to provide information, pass on experience from previous lighthouse projects and design modular solutions that are suitable for small and medium-sized enterprises (SMEs). "High-security standards, clearly defined interfaces and certified products represent the best ways to establish trust," he is convinced, emphasizing: "We aim to make it easier for our customers to access data-driven production technologies without the need for an extensive team of engineers to develop application-specific stand-alone solutions."
The Fraunhofer Institute for Production Systems and Design Technology (IPK) in Berlin has noted that more and more system manufacturers are equipping their machines with extensive sensor and monitoring systems from the outset. It is important to orient digitalization first and foremost to the configuration of the machine and to determine which process data the production machine provides automatically. According to the IPK, the machine's performance data or process parameters and settings can serve as further sources of information alongside built-in sensors and control systems.
A look at the digital solutions that grinding machine manufacturers are already offering indicates the benefits that can be obtained from using the data. The first step is always to set up a closed data space (private cloud, intranet) which is limited purely to the company itself. Open, standardized interfaces based on OPC UA are used to ensure that new grinding machines, existing machines, machines from different manufacturers, and even robots in the factory can communicate with each other and exchange data. The umati (universal machine technology interface) showcase at the GrindingHub trade fair, which the VDW (German Machine Tool Builders' Association) is organizing in Stuttgart from 14 to 18 May, will highlight the advantages in a live demonstration. Connectivity has been an integral part of the GrindingHub ever since the event’s debut two years ago. The umati initiative, launched by the VDW in 2017, is a community set up by the engineering industry and its customers. Its purpose is to disseminate and use open interface standards based on OPC UA.
Setting up a dedicated IoT
The umati partners and exhibitors at GrindingHub also include the Coburg-based company Kapp Niles, a specialist in machines for the fine machining of gears and profiles. André Wetz, Digital Transformation Project Leader, explains how a modular digital system can be structured. A standardized hardware package (consisting of sensors and an industrial PC with firewall and OPC UA server) provides the basis of the system. Customers can select the software solutions they require, such as condition monitoring of the linear and rotary axes to determine their wear, or component-specific monitoring and evaluation of the grinding and dressing processes in real-time to reduce reject rates.
Another digital solution is a closed-loop system that enables the seamless integration of processing and measuring machines. "Employees no longer need to intervene to measure the workpieces once they’ve been ground," explains André Wetz. The system ensures that data from the processing machine is transmitted directly to the measuring machine. The measurement report is returned to the machine in GDE (gear data exchange) format, which can then make any necessary corrections independently.
André Wetz emphasizes that all the solutions run on the customer’s own machines and in their own network. "This should allay any concerns about any possible loss of data sovereignty or the threat of cyberattacks from the outset," he points out. This allows customers to decide for themselves if and how they want to optimize their performance, and what benefits they want to derive from exchanging data with external parties, such as machine manufacturers or partners in the value chain. According to Wetz, it is above all Kapp Niles customers from the automotive and supplier industry that are currently benefitting from efficiency gains through digital networking. As an example of a particular application, he cites intelligent process monitoring for low-noise gearing. This can be used to identify noisy components during machining and reduce the reject rate. "This provides an effective means of meeting the quality requirements for electric vehicles," says Wetz. At the same time, however, the examples made it clear that networking across company boundaries also yields the greatest added value.
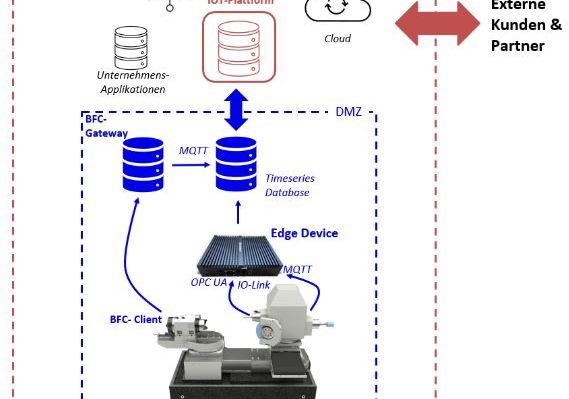
Adding value through secure cloud applications
The significant number of publicly funded research projects shows that the development of secure, cross-location cloud architectures is currently attracting considerable levels of scientific and political interest. This includes the development of a Gaia-X-compliant edge cloud system architecture, which is at the heart of the Escom (Edge Services for Components) research project. Danobat-Overbeck is also involved in the project through its collaboration with the Institute of Production Management, Technology and Machine Tools (PTW) at TU Darmstadt.
When it comes to mistrust in cloud solutions, companies are often no different to individuals. If companies have no clear idea of what happens to their data or even where it is stored, this can dampen much of the euphoria surrounding otherwise promising technologies. Edge computing is about processing and storing data in the place where it is collected. Only significantly reduced amounts of specially selected data are sent "upon invitation" to external IT instances or to the cloud via a defined interface. "This system increases security, but edge computing also enables high data transfer rates, real-time capability and data sovereignty," explains Alexej Voigt. Users retain control at all times over which data leaves the network and which does not.
Prof. Matthias Weigold, Head of the PTW at TU Darmstadt, recently wrote an article highlighting Escom's special role in the development of Gaia-X applications in the manufacturing industry. Gaia-X is a joint European project aimed at facilitating the exchange of data along the value chain, while making sure that digital sovereignty remains with the data owners and securing the interoperability of different platforms. According to Weigold, who is also a member of the WGP (German Academic Association for Production Technology – the association of leading production science academics), Escom provides key elements for Gaia-X applications in the manufacturing industry. The research project is therefore making an important contribution to defining added value and new types of product-service models.
Gaia-X – a source of hope
Gaia-X is aimed explicitly at small and medium-sized companies, too. The “Mittelstand-Digital” network lists three key advantages that a European cloud yields for SMEs: firstly, servers located in Europe are subject to European law; secondly, companies can use a European cloud data infrastructure to meet European security standards and have their performance and compliance promises confirmed by independent third parties; and thirdly, Gaia-X represents a European solution for GDPR (General Data Protection Regulation)-compliant data exchange.
It remains to be seen to what extent Gaia-X can increase trust in a cloud infrastructure. However, Alexej Voigt from Danobat-Overbeck is confident that attitudes towards data-driven production technologies can change very quickly, and he believes that sustainability could potentially become the biggest driver here. Finally, digitalization also renders production-related energy consumption transparent and enables the benchmarking of different production processes. "This could be a major step towards calculating the product carbon footprint across all life cycles," says Voigt, "and thus make a decisive contribution to promoting more sustainable production methods."