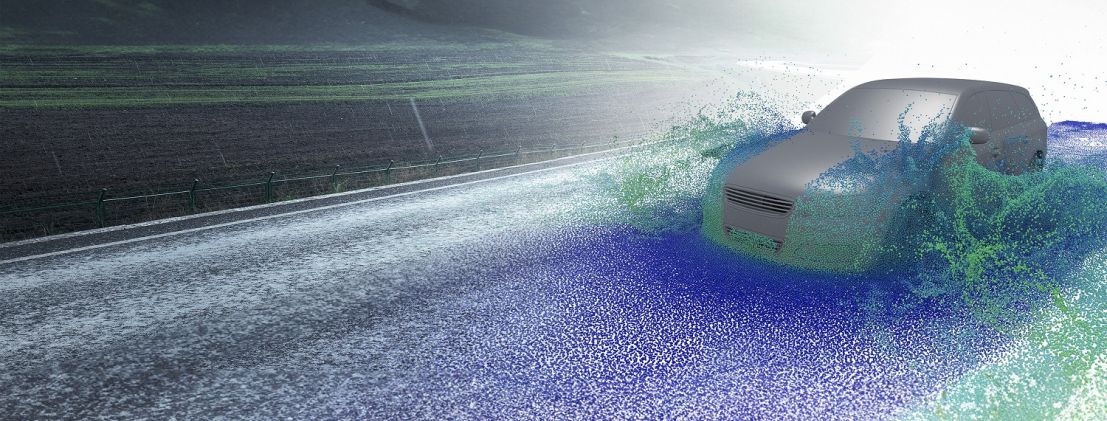
Efficient Process Simulation with MESHFREE
Simulations and digital twins are crucial to many companies, from the automotive sector to production. Because conventional software is often inadequate at modeling highly dynamic processes, researchers at the Fraunhofer Institute for Industrial Mathematics ITWM have developed a tool called MESHFREE. This solution works without a rigid computational grid, can save a great deal of time when simulating complex processes, and cuts costs.
Rigid specifications are seldom a good fit for agile processes, and what is true of organisations is doubly so for simulation methods. When modeling complex processes such as aquaplaning or virtual machining of metal, it is not possible to predict the movements of all the components and set them up in a suitable computational mesh-like those customarily used for simulations.
MESHFREE: a substitute for real-world tests
A research group at Fraunhofer ITWM was faced with this challenge over 20 years ago. “Our very first task within the project team was to simulate how an airbag would deploy in a vehicle collision,” says Dr. Jörg Kuhnert, who was already part of the group back then. “At that time, there was no way to quickly verify the safety of new developments in this field aside from costly real-world crash tests.” That is because the more objects move and interact with each other in a scenario, the more difficult it becomes to model them reliably and with reasonable levels of time and effort using traditional simulation methods.
Based on Kuhnert’s dissertation, the team — joined in 2012 by Dr. Isabel Michel focusing on Pelton turbines — developed the innovative mesh-free approach to meet this challenge. This new approach makes it possible to virtualize highly complex and dynamic situations, in some cases for the very first time. All of the team’s research findings have since been incorporated into the MESHFREE software. The result is a simulation tool with a unique selling proposition: Worldwide, no other tool makes the Generalized Finite Difference Method (GFDM) usable in industrial applications.
Flexible method for dynamic processes
Traditionally, simulations use the finite element method, in which engineers design a mesh that fits the relevant geometry and use it as a basis for computing the changes in each individual element. The initial process of setting up the mesh structure is already highly time-consuming, and frequent adjustments are required during the simulation as well. The MESHFREE software, by contrast, combines the Generalized Finite Difference Method, which it uses to solve the conservation equations of mass, momentum and energy, with efficient algorithms for solving linear systems of equations. These were developed in cooperation with the Fraunhofer Institute for Algorithms and Scientific Computing SCAI and offer a huge advantage since the cloud of numerical points used can adapt flexibly to moving geometries. This eliminates the need for laborious subsequent corrections in the computational mesh. Kuhnert and Michel received the 2024 Joseph von Fraunhofer Prize for their development, which can replace real-world testing.
From automotive to process engineering — and beyond
The award-winning method can be used for a wide spectrum of applications. One current area of focus is the automotive sector. In addition to airbag simulation, the researchers have assisted industry partners in a variety of ways to date, for example in modeling driving through water or behaviour of vehicles on sand or gravel. In process engineering, MESHFREE has helped companies optimize process parameters when working with molten glass and producing plastic parts.
Fundamentally, this method can be used anywhere a substitute is needed for measurements or experiments, or where these methods do not work well or not at all. Michel sums up: “We’re not fixated on the traditional use cases for computational fluid dynamics. MESHFREE can do much more. We deliberately kept the tool more general.” This means the software has a wealth of potential for cutting costs and saving time and material in many other fields of application as well going forward.