In the manufacture of torsion springs, extension springs, extended loop springs as well as bent parts, the WAFIOS CNC spring and wire forming systems of the FMU series are known for their good quality and performance. With the new FMU+, WAFIOS is launching a spring and wire forming system that is even more productive.
They can be used for a wide range of applications and are the first choice of many wire processing companies. Already the basic version of the spring and wire forming system is equipped with eight highly dynamic energy-efficient CNC axes that are proof of its versatility. Due to a modular structure of the machines, they can be equipped with up to 24 CNC axes so they can be optimally adjusted to customer requirements. The machines serve for the manufacture of springs and bent parts that are used in the automotive and motorcycle industry, in household appliances, in the electronics industry as well as in mechanical and medical engineering and many other industries.
Shorter set-up times and more performance
A clearly structured input mask on the multi-touch monitor guides the operator step by step: from the entry of geometry data to the allocation of tools, to the feasibility test before production up to the production of the spring's prototype. Springs are programmed by means of their actual geometry that is shown in a 3D display.
The FMU+ series has new functions, like a simulation of processes and an enhanced geometrical programming function which makes the operation of the machine even more comfortable. The standard equipment of the machines now even includes a 3-year license for iQspring+. It enables a simulation of the production sequence and automatic collision control by means of a Digital Twin.
The newly developed automatic collision control assists the machine fitter by suggesting adjustments to prevent collisions. The software itself implements different strategies with which the set-up time for complicated bent parts is considerably reduced. When a production sequence free from collisions has been found, the software will continue to optimize axis traversing paths in order to further increase the machine's performance.
The machine-independent set-up of parts at an external work station does not only increase productivity, but also allows programming activities to be bundled in a central work planning department. The program for which the ideal production parameters have been calculated is then available for the worldwide production network.
Safe axes
All servomotors of the FMU+ series have been designed as "safe axes". When protective devices are open, the machine retains the position of all axes even after being powered down. Thus the operator is able to optimize and monitor the program and production sequence at reduced speed while the protective hood is open. This function is only available when pressing the enable button on the hand-held operating device. A continuous operation of the machines at production speed is only possible when the protective devices are closed. The "Advanced set-up operation" enables the monitoring of the production process for a brief period of time at production speed by pressing the enable button on the hand-held operating device.
The use of motors with the very latest encoder systems means that the axes no longer need to be equipped with buffer batteries. Maintenance work is made easier and operational reliability is increased. Moreover, the ability to reuse tools from predecessor models safeguards compatibility within existing production installations.
For setting up the machine, the operator needs to be able to access the entire workspace to change tools and components and to carry out other set-up work. The creep-zone protection ensures that the operator cannot do this while the machine is in operation.
The well-proven and future-oriented control and drive concept from Beckhoff has been incorporated into the machines. WAFIOS has successfully used this control technology in complex tube and wire bending machines for quite some time. The automotive industry, too, very often employs this approved control technology. This creates not only supply and planning security but also security for future developments.
Customer requirements
Customer requirements were the focal point at every stage of the design and development of the new FMU+ machines. Key criteria included not only maximum output quantities, straightforward and transparent programming, and secured quality standards, but also the cost of investment. This means that whether you choose to get started with the 8-axes entry-level models or select one of the modular configuration levels which can be expanded to support up to 24 CNC axes, getting started with FMU technology will always be incredibly attractive from a pricing perspective.
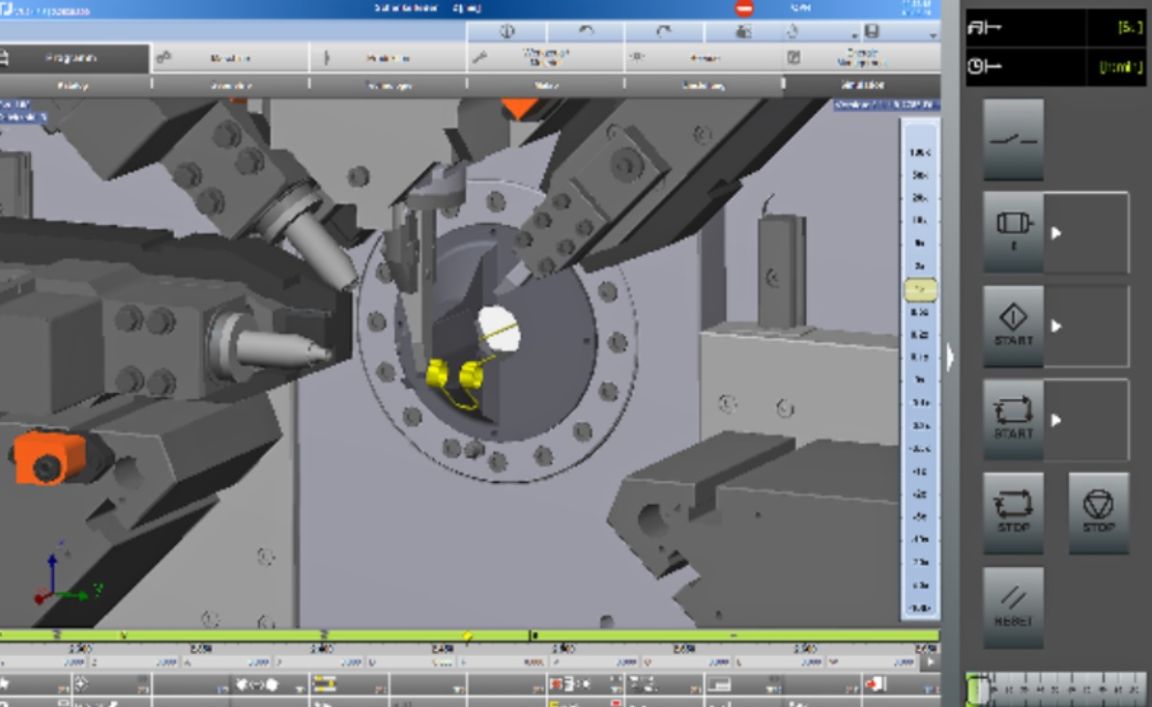
Related posts
Currently there are no news items.