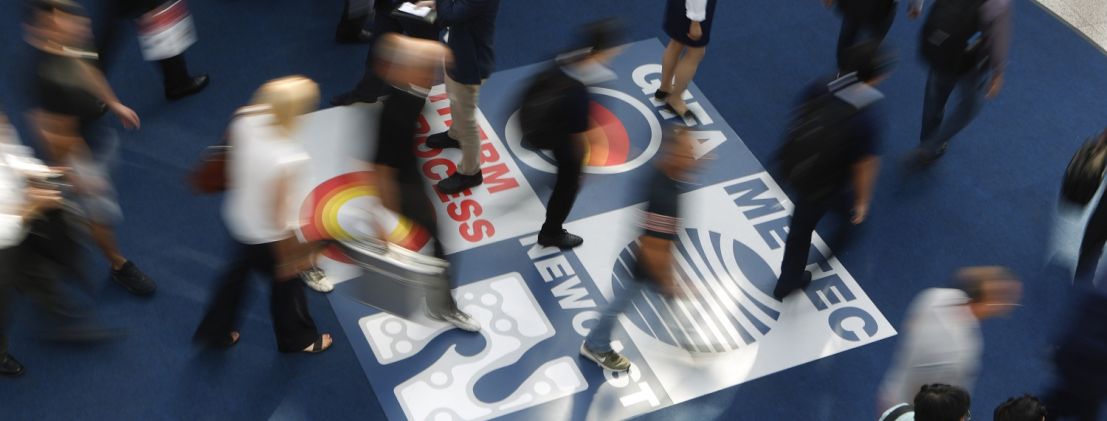
“The Bright World of Metals” kicks off with breakthrough technologies by metallurgy plant builders
Be it steel, copper or aluminium – the metal industries boast the technologies needed to achieve the climate targets. The pathways to the decarbonisation of their respective companies, however, are as manifold as are the challenges faced by steel mills and foundries, aluminium and copper smelters, forging and rolling mills. An overview of the technological spectrum of metal industries with their varying transformation paths to climate neutrality and the breakthrough technologies by metallurgical plant builders will be provided by “The Bright World of Metals” in Düsseldorf from 12 - 16 June 2023. Like every four years, Messe Düsseldorf will present the metal industry champions with their future solutions at the world’s biggest metallurgy trade fairs – at the trade fair quartet GIFA, METEC, THERMPROCESS and NEWCAST.
The metal industries maintain a key position for achieving the climate goals. The production of ferrous and non-ferrous metals accounts for some 8% of all greenhouse gases emitted globally. If the production of ores and other raw materials required for metal manufacturing are factored in, this figure amounts to around 10%.
In the focal point of decarbonisation: the steel industry
Special attention is attached to the steel industry here: to the tune of 7% of global CO2 emissions are caused by iron and steel production alone. By comparison: global road transport accounts for some 12% of all greenhouse gas emissions while approx. 11% of all CO2 emissions are caused by heating residential buildings the world over.
The good news: the technologies for decarbonisation do exist. The major metallurgical plant manufacturers SMS group, Danieli and Primetals have developed a wide range of solutions ranging from digitalisation and improvement of energy efficiency to technologies for a gradual transition to hydrogen-based, carbon-free production methods. Specialists and suppliers such as Tenova, Küttner, ABP Induction, to name but three, complement the diverse line-up of decarbonisation technologies.
Steel producers pick up the innovations and rebuild their sites for climate-neutral production. Be it ArcelorMittal or Salzgitter, Saarstahl or Tata Steel, Thyssenkrupp or Voestalpine – the progressive enterprises have “switched to green”. “Subject to the political framework, around 50% of primary steel production could be changed over to the direct reduction process, and subject to the availability of sufficient quantities of hydrogen, more than 20 million tons of CO2 could be saved every year,” says Dr. Martin Theuringer, Managing Director of “Wirtschaftsvereinigung Stahl” (German Steel Federation). Thanks to scrap-based electric steel production, he says, there is a low-CO2 manufacturing process already available today, which could be “switched” to climate-neutral in downstream processing by using green power and green hydrogen. There is a demand for “green” steel. Steel users ranging from the automotive industry to white-goods manufacturers increasingly demand climate-neutral material.
The future belongs to climate-neutral steel production with green hydrogen and power from renewable energies. Nevertheless, the paths towards reducing CO2-emissions in the global iron and steel industry are anything but uniform. The individual steel production locations vary widely by production capacity, product portfolio, and plant configuration as well as the availability of renewable energy and hydrogen – and last not least by the local political guidelines and frameworks.
The decarbonisation pathways can roughly be broken down by the terms CO2-use (SCU, Smart Carbon Usage) and CO2-avoidance (CDA, Carbon Direct Avoidance). SCU processes continue using carbon carriers for iron ore reduction and additionally rely on incremental innovations such as hydrogen injection for CO2-reduction for the conventional blast-furnace basic oxygen converter route. They also include additional environmental protection measures, so-called end-of-pipe technologies such as CCS – Carbon Capture and Storage, and CCU - Carbon Capture and Usage. CDA processes include the scrap-based electric-arc furnace route and iron-ore based steel production using natural gas for direct reduction and in future hydrogen as a reduction agent, i.e. thereby completely avoiding the use of coal or coke used for reducing the iron ores.
In Europe the focus is clearly on replacing pig iron production in CO2-intensive blast furnaces by direct reduction of iron ore in shaft furnaces using hydrogen. Largely, this transition is to be made gradually depending on the availability of (green) hydrogen. Initially, this is still done with natural gas for the most part, to which more hydrogen is added to remove the oxygen from the iron ore (reduction).
The solid iron sponge produced by direct reduction in shaft furnaces (DRI) can subsequently by processed into steel in electric arc furnaces in a hot or cold, lump or briquetted form. Another process route is fluidizing DRI in electric smelters while maintaining the downstream process for steel production with the basic oxygen converter.
Decarbonisation technologies revolve around shaft furnaces for direct reduction. DRI is primarily produced from iron ore using the Midrex and Energiron technologies. Midrex has been owned by the Japanese firm KobeSteel since the 80s; licensees of this technology include metallurgical plan builders SMS group and Primetals. Energiron is a technology developed by plant manufacturers Danieli and Tenova.
The third provider of direct reduction positioning itself in this field is a household name: Circored - the hydrogen-based fluid bed technology developed by the former Frankfurt-based Lurgi Metallurgie. Lurgi, which was taken over by the Finnish Outokumpu company in 2001, is called Metso Outotec today. The Circored process is a 100% hydrogen-based process for direct reduction of iron ore fines. A pilot plant commissioned in Trinidad in 1999 with an annual capacity of 500,000 tons had produced 300,000 tons of high-quality HBI in total. The pilot used hydrogen for process technology reasons, because the decarbonisation of steep production was not a requirement at that time. The decisive factor back then for Lurgi to develop the Circored process was a rising demand for a direct reduction process where iron ore fines could be used direct to cut production costs by eliminating a costly agglomeration step. Today, Metso can promote the Circored process as the first proven direct reduction technology for iron ore with hydrogen on an industrial scale. Primetals operates a pilot plant for hydrogen-based fine ore reduction at the voestalpine site in Linz, Austria. Hyfor direct reduction also does not require agglomeration steps such as sintering or pelletizing. The DRI is melted into liquid pig iron for the converter in the subsequent electric smelter ("smelter" from Primetals).
CO2-neutral steel mills
Once renewable energies and green hydrogen are available at competitive prices and in sufficient amounts, the combination of direct reduction and electric steel production is the ideal solution, says the leading metallurgical plant builder SMS group. Then even the construction of a new steel mill is considered, as proven by the greenfield project by H2GreenSteel at the Northern Swedish town of Boden. There the plant manufacturer erected the first CO2-neutral steel mill commissioned by a group of investors. Its Midrex-based direct reduction is to be done exclusively with green hydrogen, steel production with an electric arc furnace powered by green electricity. All other downstream processes are also based on green power. The heat treatment of the steel will no longer be done in gas-fired furnaces as before but inductively with green power. This is a lighthouse project of the European steel industry for climate neutrality.
METEC shows latest decarbonisation solutions
Most steel production sites are far from presenting the ideal conditions found in the far north of Sweden. However, there are also technologies for decarbonisation leading to climate-neutral steel production available for existing mills throughout the world. SMS promises to be the only provider of decarb solutions for really all scenarios – a focal theme at METEC.
Steel producers are opting for different avenues. The German Salzgitter AG is gradually replacing blast furnaces and basic oxygen steel converters by direct reduction (with Energiron) and electric arc furnaces, including in-house wind power and green hydrogen generation.
Competitor Thyssenkrupp is opting for another avenue. At Europe’s biggest steel production site Duisburg, the goal is also climate-neutral steel production and here too pig iron production in a blast furnace is being replaced by direct reduction; but the processes for steel production via basic oxygen converter and all other downstream processes remain unchanged.
The SMS group is replacing its existing blast furnace infrastructure by a Midrex shaft furnace for direct reduction, combined with an innovative melting technology. While still hot, the direct reduced iron (DRI) is molten down in a so-called Open Bath Furnace (OBF) energy-efficiently. Like the molten pig iron from a blast furnace, the DRI melt is fed into the basic oxygen converter and processed into steel.
With this hydrogen-operated direct reduction Thyssenkrupp wants to save more than 3.5 million tons of CO2 per year – making the combination of hydrogen-based direct-reduction plant, plus smelter and basic oxygen converter in Duisburg the world’s biggest decarbonisation project. For the SMS group this order worth over EUR 1.8 billion is the biggest single order received in the history of the company. Commissioning is scheduled for 2026.
Climate neutral with direct reduction and smelter
Plant manufacturer SMS promotes the configuration of direct reduction plant and smelter (comparable to a conventional Submerged Arc Furnace (SAF)) for both existing plants and new steel mills. In existing steel mills this equipment combination replaces the blast furnaces and associated sintering, blast heater and coking plants.
Initially, the direct reduction plant can be operated with natural gas as with Thyssenkrupp, and later the natural gas can be gradually replaced by rising percentages of hydrogen. By their accounts, the combination of a natural-gas based direct reduction plant with a smelter already reduces CO2 emissions by approx. 50% compared to the conventional blast-furnace route. This is achieved by the higher hydrogen content in natural gas. In a second step the natural gas can be gradually replaced by hydrogen as a reduction gas, which makes it possible to reduce CO2 further up to approx. 65%.
SMS promises that the smelter is not sensitive to low-quality ore thanks to the reduction process. In addition to hot sponge iron, the charge material for the smelter can even contain up to 10% compressed or loose scrap. The OBF can also produce slag. Like blast-furnace slag, this slag can be granulated and used in the cement industry.
Many ways – one goal
Due to the long investment cycles for metallurgical plants, a large part of future CO2-savings must be obtained by refitting existing plants and even at locations where neither hydrogen nor natural gas are available in sufficient amounts. “Climate protection and efficiency must go hand in hand to produce real, long-term effects and successes,” says Burkhard Dahmen, CEO of the SMS group. On other markets and in other regions such as India and China, he adds, alternatives for direct reduction are needed.
Steel production can be decarbonised by the introduction of innovative, integrated process solutions both in new plants and in existing ones. An important step towards climate neutrality here is the installation of additional infrastructure for using sustainable and renewable energy carriers such as hydrogen, biomass or green power. The “last mile” towards climate-neutrality can then be covered by technologies for carbon capture and storage.
Bridge technology (1): Blue Blast Furnace
Plant manufacturer SMS promises to reduce CO2 emissions up to 28% by refitting conventional blast furnaces with the so-called Blue Blast Furnace technology. The special characteristic of a “blue” blast furnace is the production of syngas from the process gases of blast furnaces and coking plants and its injection into the bottom part of the blast furnace via a novel hot blast ring duct. The syngas is composed mainly of carbon monoxide and replaces coke as a reduction agent to reduce the iron charge in the shaft.
Syngas can be produced with a variety of technologies. A novel reforming process by the SMS subsidiary Paul Wurth is considered especially efficient here. During dry reforming of coke furnace gas, the cupola gas from the blast furnace and the coke furnace gas are reformed at high temperatures. Since this process only uses waste gas from the metallurgical plant and no longer requires any coal, it holds a high potential for reducing CO2. Alongside, there are further technologies to produce syngas, e.g. the reforming of natural gas or coke furnace gas and tar.
Bridge technology (2): blast furnace upgrade with EasyMelt at METEC
Based on the Blue Blast Furnace principle but going beyond its emission-reduction potential, SMS will present the so-called EasyMelt process (Electric Assisted Syngas Smelter) at METEC. This technology is an electrified direct reduction and melting process where the hot blast from the conventional blast-furnace process is replaced completely by such gases as coke gas, natural gas, hydrogen and ammonia with the help of a small quantity of coke. By SMS accounts, depending on the energy applied, this technology can save over 60% emissions compared to the conventional route comprising blast furnace and basic oxygen converter. The remaining direct emissions can be further reduced by using CCS technologies or by using biomass or biogas as a base material. For refitting existing plants EasyMelt is less capital-intensive in comparison with all other technologies for low-CO2 iron production. Unlike a direct-reduction only plant, EasyMelt can also process conventional iron ore and not only the scarce and expensive iron ore pellets or lump ore with high iron content, thereby promising economic plant operation. By company accounts, this technology represents an economic alternative to the direct reduction route. Similar to the Blue Blast Furnace technology, EasyMelt can be introduced gradually.
Foundries
The many small and medium-sized outfits in the foundry industry are also too heterogeneous for a one-fits-all strategy to produce effects. However, all companies share one concern: energy. “The crucial criterion for transformation is how the high energy needs of foundries can be satisfied in a climate-neutral way,” says Prof. Dr.-Ing. A. Bührig-Polaczek, Head of the Foundry Institute at the RWTH Aachen University. This refers to the energy-intensive melting technology, on the one hand, and to the entire casting process including upstream suppliers and customers, on the other, he adds. “The technologies are largely available,” says the foundry expert.
“For melting and holding, for example, established electric furnaces are available,” says Polaczek. “But hydrogen as a new energy carrier is also technically fit for melting and holding. Although the technology for hydrogen is generally ready, there are still some development and optimisation efforts needed.”
GIFA and THERMPROCESS: fireworks display of technological innovations
New burner technologies for natural gas (for the time being) but hydrogen-ready form one of the focal themes at the trade fairs GIFA and THERMPROCESS. What is already feasible here, will be demonstrated by amongst others Küppers Solutions with its innovative dual-fuel recuperator burner iRecu. This development promises efficient heat recovery, maximum fuel flexibility and a CO2-neutral production. This invention was awarded with the Innovation Prize for Climate and Environment 2022 and before with the Efficiency Prize NRW 2019. It is also an excellent example of the strengths of new manufacturing technologies. The recuperation burner is the world’s first burner manufactured by 3D printing in series – and could only be manufactured additively.
Other focal themes at the world-leading trade fairs GIFA and THERMPROCESS include innovations in induction melting units and thermal process technologies, as showcased by the major industrial furnace manufacturers ABP Induction and Otto Junker. They, too, focus on energy efficiency and savings. Induction technology is of particular importance in view of zero-carbon emitting induction smelters as a replacement for cupolas and gas-fired furnaces. Technologies and concepts for heat recovery and use of renewable power generated by additional PV systems are also key developments on the pathway to climate neutrality. In addition, induction furnaces are increasing in importance for metal recycling. One goal is the ability to use as much organically contaminated aluminium scrap as possible in foundries.
Foundries do make use of plant manufacturers’ innovations. Overall, foundry expert Bühring-Polaczek can give the industry a “good report”: “Most companies are already active in the optimisation and transformation of their complete foundry process chain and can already point to first successes.” An important way into the future, he adds, is the consistent digitalisation of processes along the lines of Industry 4.0. “It allows companies to gain a new, facts-based transparency for even complex processes, and, hence, considerable efficiency gains,” the professor sums up.
This is why foundry expert Bührig-Polaczek appeals to policy makers: “While companies and foundries are advancing speedily, the reliable availability of climate-neutral energy remains an open issue to be solved on a political level. This delays or impedes many necessary innovations and investment.”