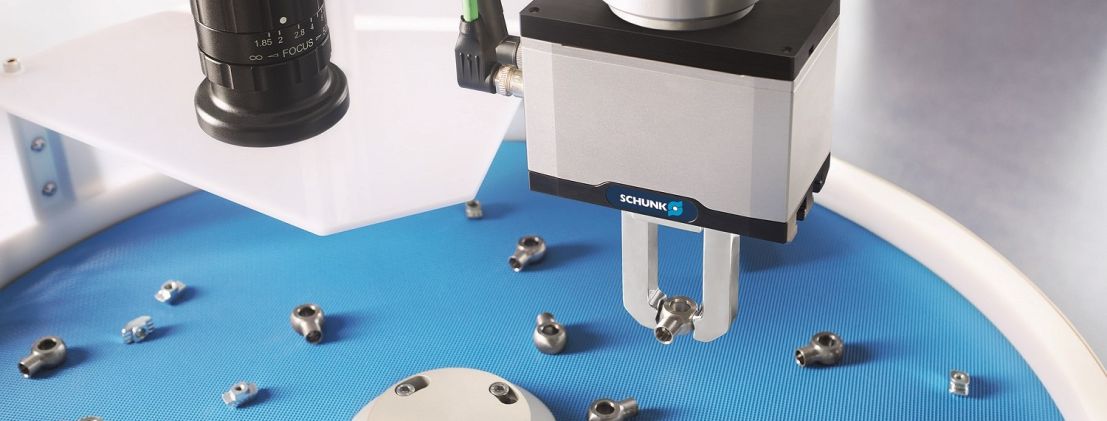
Schunk comes up with 2D Grasping kit for vision-based gripping
Linking mechanical and logical gripping has now been made simple. Automation specialist Schunk has, in fact, developed the 2D Grasping Kit for handling individual objects randomly arranged on one plane. The core of this intelligent system is its in-house developed AI software, which is pre-installed on Schunk's own industrial PC (SVC). This fully coordinated package of hardware, software and service stems from one source and can be used for all robots.
The removal of individual randomly arranged and non-positioned parts from a conveying belt, tray or staging table is a common operation in many industrial manufacturing operations. They are then usually further processed, separated or carried to a machine - manually or automatically. Automated handling using robots, grippers and vision systems is demanding and requires experience in image processing, lighting and process technology. With the 2D Grasping Kit, Schunk is now offering a complete solution that makes it much easier to get started with automated object handling. Users can easily integrate the plug-and-play, vision-based system and implement automation straight away. Companies that are still in the early stages of automating their manufacturing processes in particular will benefit from this. No prior knowledge of programming or image processing is required. Complete compatibility of all components emphasizes the user benefit - Schunk acts as a single point of contact for the entire solution.
The core of this is the Schunk-KI software
Following on from the MTB application kits for simple partial automation of machine loading and unloading, the 2D Grasping Kit is a further module with which automation expert Schunk is offering its customers a concrete solution for greater efficiency and productivity. The kit combines intelligent object recognition and flexible gripping with intuitive usability and can be customized to meet specific customer requirements. This fully coordinated automation solution for gripping and depositing non-position-oriented workpieces consists of a camera system including a lens, an application-specific gripping system, Schunk's own industrial PC (SVC) and a plug-in for easy integration into the robot control system. The core of the system is the AI software developed by Schunk, which ensures reliable recognition, even under changing light conditions. All components in the kit are precisely matched to each other and are process reliable.
Automated to optimal grip
The camera system reliably detects workpieces on a defined plane, even in awkward lighting conditions, while calculating possible grips together with collision checks. The workpieces no longer have to be sorted or positioned in advance; users can retain their own earlier processes. Workpiece detection uses AI to search for previously defined objects. The software calculates how the workpiece can be gripped without any collisions in the defined workspace using the interference contours of the fingers and the workpiece previously defined in the software. After detection, collision-free grips and approach points are calculated automatically and transferred to the robot in a matter of seconds. In doing his, Schunk has incorporated its many decades of experience in automated gripping planning.
The user can integrate the 2D Grasping Kit into various robots or cobots, regardless of manufacturer, by means of ready-made software modules; Schunk supplies the appropriate plug-in for the robot in the kit. During conversations with the customer and while defining their requirements, a combination tailored to the application is assembled and validated. Depending on the gripping situation, suitable grippers can be combined for each cobot type - electric, magnetic, adhesive or pneumatic. Using the Calculation and Sizing Assistant gripping by Schunk and realistic validation in the CoLab robot application center, it is possible to check exactly how well the selected gripper can grip the workpieces prior to its application.
With the 2D Grasping Kit, users from many industries realize pick & place applications of randomly arranged parts on a single level - for example from a vibrating table, assembly line or load carrier. The metalworking industry, the automotive sector, companies in production engineering and logistics as well as from the life-science sector gain reliability, process precision and benefit from higher output using the kit-manual, error-prone handling thus becoming a thing of the past. Valuable personnel resources can therefore be used for more complex and less monotonous tasks. The kit can be used in both clean and lightly soiled production environments.
Validation of the application in the CoLab
In the CoLab, the Schunk Robot Application Center, the 2D Grasping Kit can be extensively tested and validated on the actual application. For example, it is possible to determine how reliably the workpieces are detected by the camera and whether the pickup and placement of the workpieces functions using a reliable process. In addition, the customer receives significant support in implementing their tasks or teaching their first workpieces. This makes it much easier to find the appropriate application solution tailored to requirements, minimizes risks and accelerates the introduction of the automation solution.
Related posts
Currently there are no news items.